A deep groove ball bearing stands as a cornerstone in the mechanical world, renowned for its versatility and reliability. This type of bearing is prevalent across various industries due to its unique design that supports radial and axial loads efficiently, making it a top choice for applications needing smooth and unobtrusive operations.

Experience in using deep groove ball bearings reveals their impressive longevity and operational quietness — two critical factors for their widespread acceptance. Over the years, engineers have gravitated towards these bearings for their ability to reduce noise and vibration in applications ranging from home appliances to automotive systems. In practice, a washing machine equipped with a high-quality deep groove ball bearing tends to operate with a noticeable reduction in noise compared to one using inferior bearings, enhancing user satisfaction and prolonging machine life.
From an expertise standpoint,
understanding the technical aspects of deep groove ball bearings is crucial. These bearings consist typically of an inner and outer ring, a series of balls, and a cage to evenly distribute and maintain the spacing of the balls. This architecture allows them to maintain high-speed operations with minimal friction. The precision in manufacturing these components is pivotal; even minor deviations can significantly impact performance. Engineers must prioritize quality control and utilize advanced materials to produce bearings that withstand the rigors of demanding environments.
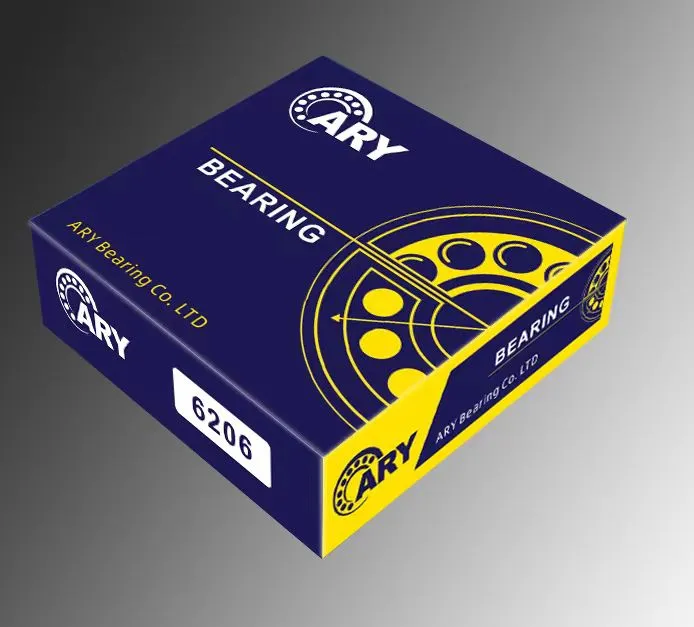
The authoritativeness of deep groove ball bearings in the market is unmatched, underpinned by a century of development and deployment across various sectors. Their significance is not merely historical; ongoing advancements continue to push the boundaries of what these bearings can achieve. Leading manufacturers consistently invest in research and development to innovate within the confines of their tried-and-true design. For instance, modern variations might incorporate ceramic balls to reduce weight and increase speed capability, addressing niche demands in aerospace or precision machinery sectors.
a deep groove ball bearing
Trustworthiness in the context of deep groove ball bearings is validated through rigorous testing and quality certifications. Trust is further established through detailed product documentation, which includes load ratings, expected lifespan, and maintenance guidelines. This level of transparency allows end-users to make informed decisions and understand the operational parameters. Furthermore, renowned brands offer comprehensive warranties and support, reinforcing consumer confidence in their products.
In product selection, the application-specific demands should guide the choice of a deep groove ball bearing. Considerations such as load capacity, speed limitations, and environmental conditions are crucial. For instance, high-speed applications like electric motors benefit from deep groove ball bearings with precision-grade tolerances. They deliver the requisite speed while minimizing heat generation, a critical factor in preventing premature bearing failure. Conversely, for applications subjected to corrosive environments, stainless steel or specially coated bearings can offer enhanced resistance and longevity.
In sum, deep groove ball bearings are an indispensable component in the mechanical realm, celebrated for their robustness and versatility. Accumulating decades of expertise, they are trusted by engineers and appreciated for their ability to quietly and efficiently enhance the lifespan of numerous applications. As innovations continue to refine their qualities, the role of these bearings in future mechanical design remains as pivotal as ever, ensuring their legacy endures in the pantheon of engineering marvels.