Deep groove bearing balls are vital components in many mechanical applications, characterized by their ability to support both radial and axial loads while maintaining high rotation speeds. Crafted with precision and held to stringent quality standards, these components are integral in machinery ranging from household appliances to high-performance motorsport engines. Understanding the nuances of these components can enhance not only their application but also prolong the life and efficiency of the machinery they inhabit.

When selecting deep groove bearing balls, expertise in materials and design is essential. Typically manufactured from high-grade steel or ceramic, the choice of material affects not just the bearing’s performance but its longevity and operational temperature thresholds. Steel bearings are renowned for their robustness and affordability, making them a staple in industries where durability is paramount. Conversely, ceramic bearings, though more expensive, offer a significant reduction in weight and increased resistance to thermal expansion, making them ideal for precision applications where minimizing wear and tear is crucial.
One cannot overlook the importance of lubrication in the operation of deep groove bearing balls. Proper lubrication reduces friction, prevents overheating, and minimizes wear, thus extending the operational life of the bearings. Oil and grease are the two primary lubricants used, each suitable for different environments and performance requirements. For example, oil lubrication is often preferred in high-speed applications due to its ability to dissipate heat more effectively. On the other hand, grease lubrication is advantageous in environments where bearings are exposed to contaminants, as it provides a protective barrier that helps maintain cleanliness.
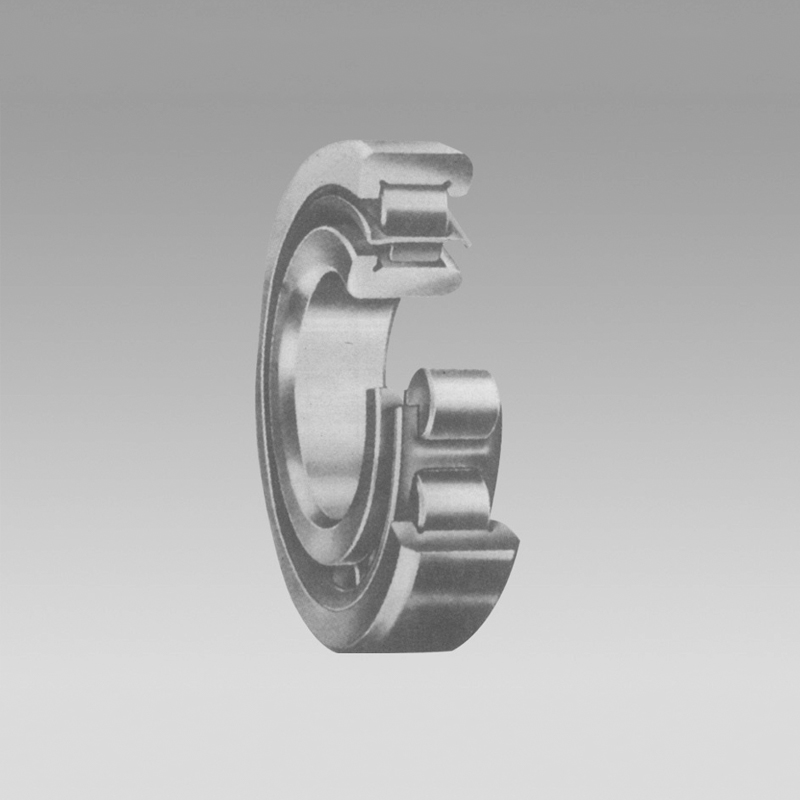
Authoritativeness in the context of deep groove bearing ball innovation is best seen in the manufacturing processes that ensure precision and quality. Modern manufacturing techniques employ advanced heat-treatment processes and computer numerical control (CNC) machining to achieve tolerances within microns. This level of precision ensures that the rolling elements are perfectly spherical, thereby reducing vibration and noise during operation. Furthermore, manufacturers often perform rigorous testing under extreme conditions to certify their products' reliability and performance, providing consumers with confidence in their investment.
bearing ball deep groove
Real-world experience in using deep groove bearing balls highlights their versatility across multiple sectors. In the automotive industry, for example, these bearings are crucial in gearboxes due to their ability to handle both radial and thrust loads. Similarly, in the aerospace sector, where reliability and efficiency are non-negotiable, the lightweight properties of ceramic bearings offer significant advantages, reducing aircraft weight and, consequently, fuel consumption. Moreover, hobbyists and engineers alike leverage the precision of these components in robotics, where micro-movements demand exceptional accuracy.
Trustworthiness of a deep groove bearing ball supplier is established through transparency and customer support. Trustworthy suppliers provide comprehensive information on product specifications, material safety data sheets (MSDS), and technical support to aid in product selection and maintenance. Additionally, certifications such as ISO 9001 or AS9100 are indicators of a company's commitment to quality management and continuous improvement. Choosing a supplier with these credentials can assure customers that they are receiving products that meet or exceed industry standards.
Emphasizing expertise, real-world application, and manufacturing precision, deep groove bearing balls are indispensable in various fields, demonstrating an intersection of engineering excellence and practical performance. These components represent more than just mechanical elements; they are the unsung heroes that enable technology and machinery to function with the reliability and precision that modern industries demand. With advancements in materials and technology, the future of deep groove bearing balls is poised for even greater innovations that will redefine industry benchmarks.