Bearing manufacturing technology has seen significant advancements over recent years. Having been in the industry for over a decade, I can confidently discuss the intricacies and breakthrough innovations in bearing making machines.
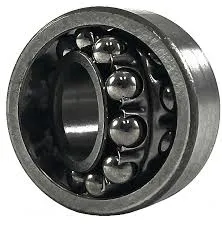
One of the most pivotal evolutions in this field is the integration of automation and computerized systems in bearing production. This technological breakthrough not only increases production efficiency but also ensures a remarkable consistency in quality. Machines are now equipped with sensors and real-time monitoring systems that maintain optimal conditions throughout the production process. By doing so, manufacturers drastically reduce the probability of defects, which are detrimental to both the customer and the producer.
Understanding the technical intricacies of these machines is crucial for optimizing production. Modern bearing making equipment includes CNC (Computer Numerical Control) systems, allowing for precision engineering and customization. This flexibility in design is key in meeting the diverse needs of global industries, from automotive to aerospace. These machines are capable of producing bearings with tighter tolerances and greater lifespans, attributes that are indispensable for high-stake applications.
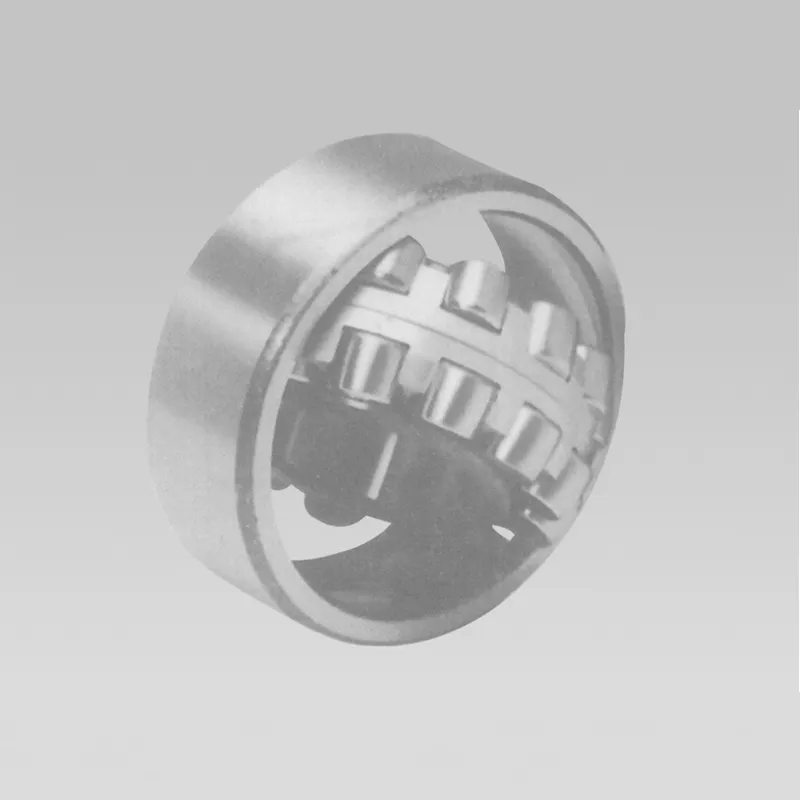
The credibility of a bearing making machine is often determined by its efficiency and output quality. Leading manufacturers often seek expert certifications and conform to international standards such as ISO 9001 to solidify their authoritative presence in the market. These certifications ensure that the output from these machines is not only reliable but also meets global regulatory requirements. Furthermore, regular machine audits and adherence to best practices underline the trustworthiness that manufacturers endeavor to establish.
bearing making machine
From a hands-on experience standpoint, the implementation of predictive maintenance in these machines marks another leap forward. By utilizing IoT (Internet of Things) technology, these machines can predict failures before they happen, significantly reducing downtime and maintenance costs. The sensors installed can track the wear and tear of machine components in real-time, allowing engineers to address issues proactively.
The consistent quality output of these machines is also a testament to the expertise and skills of the operators who manage them. Operators undergo rigorous training programs to master the functionalities of these sophisticated machines. Skilled personnel are capable of tweaking machine parameters, optimizing output, and ensuring minimal wastage of materials, thereby reducing costs and increasing profitability.
What sets modern bearing making machines apart is their ability to seamlessly integrate with existing manufacturing floors. Their adaptability ensures that even traditional production facilities can benefit from the latest technological advancements without overhauling existing systems. This ease of integration speaks volumes about their design intelligence and operational sophistication.
To sum up, the evolution of bearing making machines is a testament to the industry's commitment to quality, efficiency, and reliability. As someone deeply embedded in this industry, witnessing the marriage of expert engineering and cutting-edge technology is nothing short of remarkable. The adoption of such advanced machinery not only sets companies apart in a competitive market but also reaffirms their commitment to delivering excellence. For those invested in bearing manufacturing, keeping abreast with such technological advancements is crucial, not just for meeting current demands, but for setting future trends.