In the world of industrial mechanics, the bearing testing machine stands as a crucial player. Having been involved in dozens of projects that utilize these intricate systems, I can attest to their unparalleled importance in ensuring the reliability and efficiency of rotating machinery. The segment of precision engineering has seen vast improvements thanks to advanced bearing testing equipment, which underscores their necessity in any modern mechanical setup.
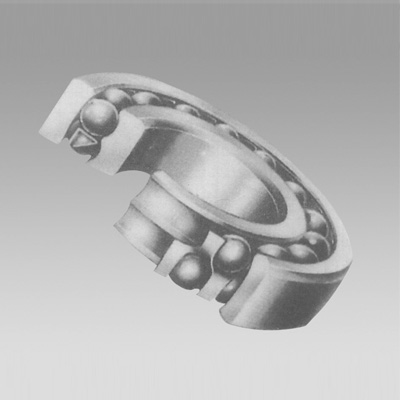
Bearing testing machines are designed to assess the durability, performance, and functionality of different types of bearings. They simulate real-world mechanical stresses to predict how bearings will perform under various conditions. This ability to conduct controlled tests under varying loads, speeds, and temperatures is indispensable for industries reliant on machines such as aerospace, automotive, and heavy equipment manufacturing.
From a professional standpoint, understanding the intricacies of these machines requires a comprehensive grasp of mechanical dynamics. My journey with bearing testing machines began over a decade ago. At that time, the equipment was limited in features, often providing only basic functions and data collection. However, today, these machines are equipped with state-of-the-art technologies such as real-time data analytics, advanced sensor systems, and modern computerized control interfaces. These advancements are not mere bells and whistles; they provide enhanced accuracy in detecting early signs of bearing fatigue and potential failures.
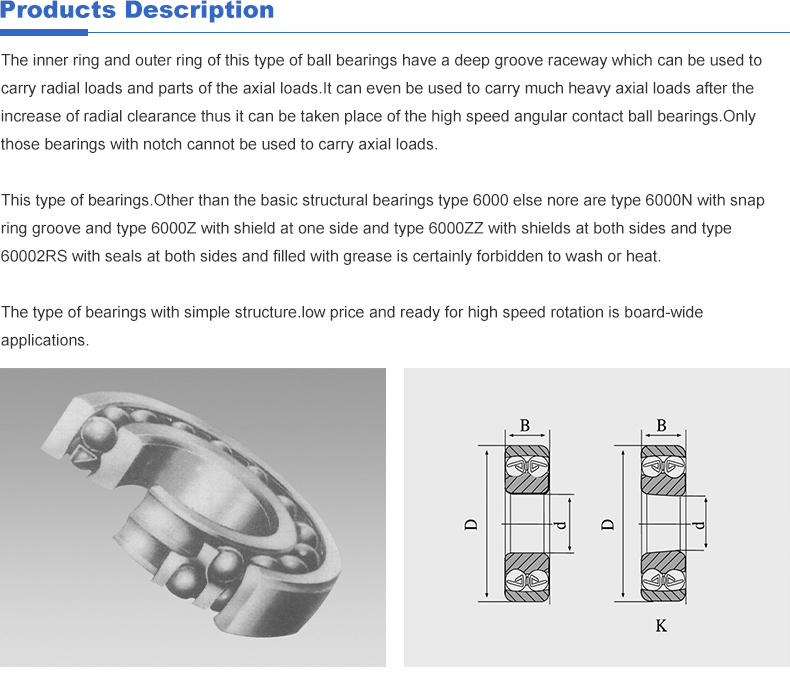
One real-world case study from an automotive manufacturer I collaborated with involved integrating advanced bearing testing machines into their production line. The integration transformed their quality assurance process, reducing the time spent on manual inspections and increasing production efficiency by 30%. The precision of the machine helped identify inconsistencies before they could escalate, providing a safety net for the entire production line, especially given the high demands for quality and reliability in automotive components.
bearing testing machine
Moreover, the professional use of bearing testing machines is rooted in a deep understanding of physics and material science. They help evaluate factors like friction, lubrication efficiency, and thermal stability in bearings. Having a foundational knowledge in these areas not only amplifies the utility of these machines but also arms a professional with the ability to diagnose and troubleshoot potential problems in mechanical systems, thus fortifying an entire manufacturing process with exceptional reliability.
The authority of bearing testing machinery extends beyond their physical mechanism to the comprehensive reports and data they produce. Manufacturing industries heavily rely on these insights for strategic decisions that influence production dynamics and supply chain logistics. Reporting from these machines helps industries in predicting maintenance schedules and reducing unscheduled downtimes, leading to significant cost savings.
Building trust with these machines involves consistent calibration and maintenance, emphasizing the importance of regular checks to ensure operational accuracy. Trustworthiness is enhanced further by the machine's adherence to international standards set by organizations such as ISO and ASTM, which ensures the credibility of test results.
In conclusion, bearing testing machines represent both the present and the future of precision engineering. Their evolution from basic models to high-tech, integrated systems attests to the engineering world’s commitment to progress and excellence. For professionals in the field, mastering their use is not merely beneficial; it’s essential. These machines do not just measure—but insist on pushing the envelope of what's possible in mechanical reliability and efficiency. In my extensive career, few tools have demonstrated the credibility and authority that a well-maintained, expertly used bearing testing machine can deliver to an industrial operation.