Deep groove ball bearings have long been a staple in industries ranging from automotive to aerospace, owing to their simple yet efficient design. These bearings are characterized by their ability to support both radial and axial loads, making them versatile components in mechanical systems. However, like any engineering solution, they offer a range of benefits and drawbacks that merit consideration when selecting the appropriate bearing type for specific applications.
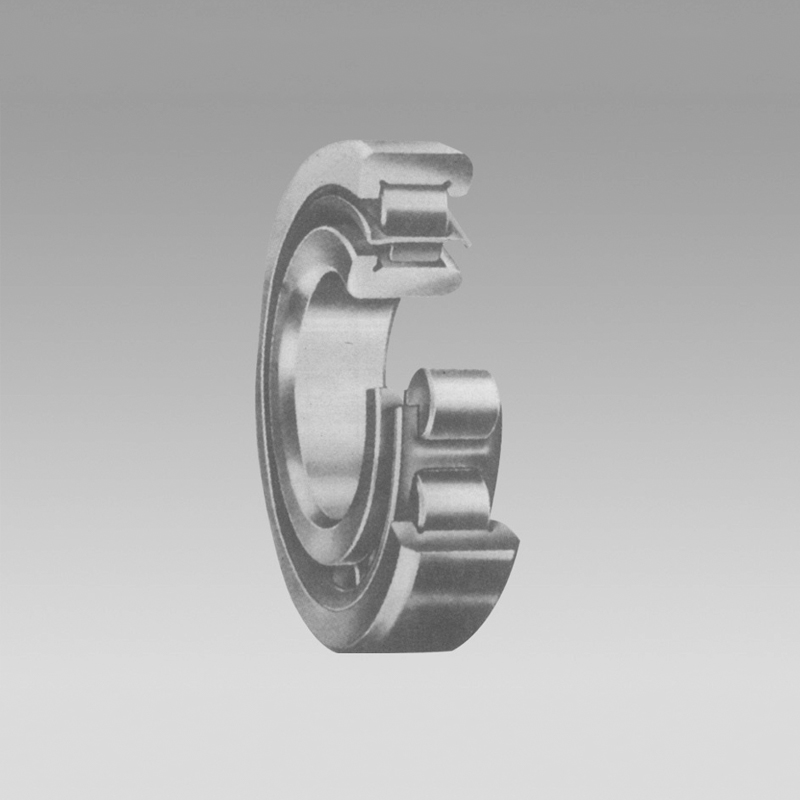
One of the primary advantages of deep groove ball bearings is their capability to operate at high speeds. The design ensures minimal contact friction within the bearing, enabling machinery to function efficiently without overheating - a crucial factor in high-speed applications. Coupled with this is their durability; manufactured with precision to handle considerable stress, these bearings exhibit a prolonged service life even under continuous operational load. This longevity translates to reduced replacement costs and lower maintenance frequency, which is economically beneficial for industries seeking reliability.
Their simplicity also underscores another advantage easy installation and minimal maintenance. Deep groove ball bearings are constructed with straightforward geometry, allowing for easy integration into a wide range of mechanical configurations. This streamlined design reduces the time and expertise required for installation, making them accessible even to those with limited technical knowledge. Additionally, their ability to handle misalignment to a certain degree further enhances their desirability, as they can accommodate minor imperfections in shaft alignment without compromising the overall performance of the machinery.

In terms of operation, these bearings excel in facilitating noise reduction. The rolling elements within deep groove bearings, typically made of steel or ceramic, are engineered to interact smoothly, mitigating vibration and noise generation. This characteristic is particularly advantageous in industries where quiet operation is paramount, such as medical equipment or home appliances. Their sealed design often ensures cleanliness, protecting against contaminants that might otherwise lead to premature wear or failure.
Despite these strengths, there are notable limitations to deep groove ball bearings. They are generally not suited for applications involving heavy axial loads. Their design inherently favors radial support, and while they can tolerate some axial force, excessive pressure in this direction can lead to reduced performance and increased wear. Hence, for applications where axial loads dominate, alternate bearing types may be more suitable.
deep groove ball bearing advantages and disadvantages
Moreover, heat generation remains a concern. Although they operate well at high speeds, prolonged high-speed utilization can elevate temperatures within the bearing. Without adequate cooling or lubrication, this can degrade the lubricant properties, leading to increased friction and potential failure. Therefore, careful consideration must be given to operating conditions to mitigate thermal-related issues.
Additionally, while the bearings’ sealed design helps in keeping debris out, it also complicates the re-lubrication process. In certain applications, the inability to easily apply fresh lubricant can reduce bearing lifespan, necessitating complete replacement instead of simple maintenance.
Deep groove ball bearings are also susceptible to overload. In scenarios where unexpected loads occur, such as in heavy machinery subject to shock loads, the bearings can suffer irreversible damage. It's crucial for engineers to calculate load conditions accurately to avoid this pitfall.
Balancing the advantages against the disadvantages of deep groove ball bearings requires a nuanced approach. Application-specific analysis, considering load types, operating environments, and maintenance capabilities, ensures the optimal selection of bearing type. By leveraging their efficiency and managing their limitations, these bearings provide an effective solution in a myriad of industrial applications, reinforcing their status as a fundamental component in mechanical systems. For users, this means that while these bearings offer numerous benefits, understanding their operation and limitations is key to maximizing performance and extending service life.