Understanding the specifics of deep groove ball bearing cross-section details can be the key to unlocking optimal performance in high-demand applications. When it comes to choosing the right type of bearing for machinery or equipment, the configuration and cross-section of deep groove ball bearings play a pivotal role.
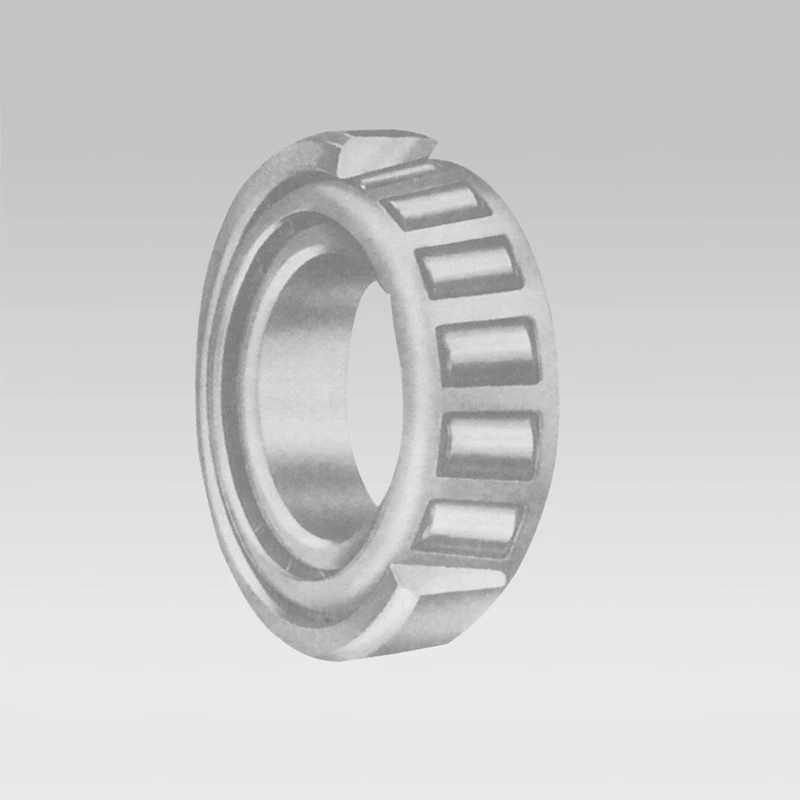
Deep groove ball bearings are a fundamental component in a multitude of mechanical industries due to their versatile capabilities. They are designed to support radial and axial loads, which allows them to function effectively in both stationary and dynamic operations. The cross-sectional design of these bearings is a critical aspect influencing their efficiency, durability, and performance.
A deep groove ball bearing comprises several essential elements an inner ring, an outer ring, a cage, and a set of metal balls that roll between the two rings. The cross-section of the deep groove ball bearing is characterized by the profound grooves on the inner and outer rings which encapsulate the balls. This groove geometry is precisely engineered to reduce rotational friction and support high speed, combined with better load distribution.
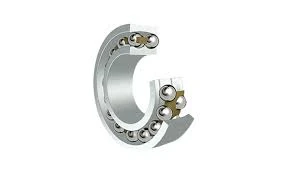
Being aware of the depth and design of these grooves can provide crucial insights into the bearing's capabilities and applications. The depth of the grooves influences the stability and precision of the machinery in which they are installed. A deeper groove allows the bearing to accommodate more significant radial loads, which is indispensable for high-speed environments where these bearings are often employed.
Manufactured with stringent quality control, deep groove ball bearings feature low torque and are capable of operating at high speeds with minimal noise and vibration. This makes them ideal for electric motors, automotive applications, and household appliances where seamless operation is paramount. Quality control during production ensures that each bearing boasts a geometric precision that maximizes efficiency and prolongs its operational lifespan.
A crucial aspect of deep groove ball bearings is their lubrication regime, which significantly influences their performance. Proper lubrication reduces friction, wear, and helps to dissipate heat generated during operation. This maintenance aspect emphasizes the importance of understanding the lubrication requirements compatible with the bearing's material and the operational environment.
deep groove ball bearing cross section
Selecting the appropriate deep groove ball bearing involves assessing its load-carrying capacity, rotational speed capability, and thermal properties. Engineers and technicians prioritize bearings with special seals or shields to prevent contaminants from entering their delicate internal environments, thereby ensuring consistency in performance and durability.
In more advanced applications, customized bearings with specific cross-sectional dimensions can be designed to meet unique requirements. This customization allows for optimized light-weighting in aerospace applications or reinforced load capabilities in industrial machinery.
Understanding these cross-section details is not only beneficial but imperative when selecting a bearing for specific applications. They provide insights into the bearing's physical interactions during operation and allow engineers to predict how it will behave under diverse conditions.
Knowledge of advanced material science and engineering combined with practical hands-on experience results in a tailored solution that leverages the unique properties of deep groove ball bearing cross-sections to enhance overall system performance. For professionals who integrate these bearings into their machinery, understanding these intricacies adds significant value, ensuring the reliability and efficiency of the final product.
Moreover, learning to interpret these specifications and choosing the right cross-section aligns with building trust and authority within the industrial field, emphasizing reliability and expert decision-making capability. Consequently, the deep groove ball bearing cross-section is not a mere structural detail but a testament to quality engineering and operational success.