Deep groove ball bearings represent sophisticated pieces of engineering, integral to numerous applications across various industries. Known for their durability, versatility, and efficiency, these bearings play a critical role in ensuring operational smoothness and longevity. The hallmark of deep groove ball bearings lies in their design, optimized for minimizing friction while supporting both radial and axial loads. Here, we delve into the intricacies of deep groove ball bearing design, underlining the principles and innovations that solidify their esteemed status in the mechanical engineering realm.
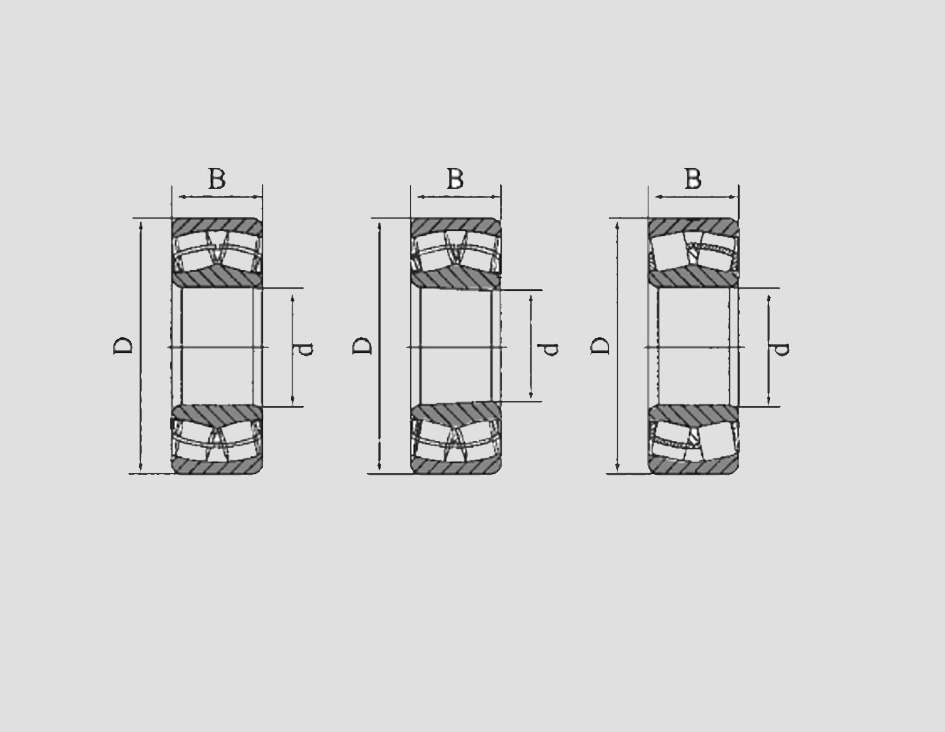
At the heart of the deep groove ball bearing design is the geometry of the inner and outer rings, which are crafted with raceway grooves. These grooves help in reducing operational friction by allowing balls to fit snugly within the concave surfaces, maintaining optimal alignment under various load conditions. This precision in design ensures minimal contact area, enhancing efficiency by reducing resistance during high-speed rotations.
The material choice for deep groove ball bearings is another cornerstone of their design. Typically constructed from high-grade chromium steel, these bearings are engineered to withstand immense stress and resist wear. This choice of material is not arbitrary; it's a product of meticulous research aimed at optimizing load capacity while minimizing wear and tear. Advances in metallurgy have further allowed the incorporation of hybrid designs using ceramic balls, which offer superior performance by reducing weight and enhancing speed capabilities.

Seals and shields in deep groove ball bearings play a fundamental role in their effective operation. These components protect the interior mechanism from contaminants, such as dust and moisture, that could otherwise degrade performance. The design considerations for seals and shields are focused on balancing protection with operational efficiency, ensuring that they do not introduce additional friction while maintaining an effective barrier.
In the ever-evolving landscape of mechanical engineering, innovation in lubrication technology has markedly influenced the design of deep groove ball bearings. Modern designs incorporate advanced lubricants that reduce heat generation and further minimize friction. Seal-integrated lubrication systems have become increasingly prevalent, providing continuous lubricant flow and thereby extending the lifespan of the bearings even under high-load conditions.
deep groove ball bearing design
Advanced computational tools like Finite Element Analysis (FEA) have revolutionized bearing design by allowing detailed simulation of performance under varied conditions. These tools enable precise calculations of stress distribution across bearing components, facilitating the production of bearings tailored for specific operational environments.
Deep groove ball bearings demonstrate exceptional versatility, finding applications in industries ranging from automotive to aerospace. Their design must therefore accommodate diverse operating conditions, environments, and performance requirements. This adaptability is achieved through variations in design that include differences in size, material, and internal clearances.
A consideration of deep groove ball bearing design would be incomplete without acknowledging the continuous pursuit of sustainability in manufacturing processes. Responsible sourcing of materials, energy-efficient production methods, and design strategies aimed at recyclability are now integral to the development process. These practices are not only essential for environmental compliance but also enhance the economic viability of deep groove ball bearings by reducing overall lifecycle costs.
In conclusion, the design of deep groove ball bearings is a culmination of centuries of engineering refinement, underscored by innovation and precision. Their continued relevance and success across myriad applications stem from rigorous design principles that emphasize efficiency, durability, and adaptability. For professionals in industries reliant on machinery parts that exemplify these qualities, understanding and selecting the right deep groove ball bearing design is pivotal. As technology evolves, the industry can anticipate further enhancements in design and material technology, promising even greater performance and longevity for future generations of deep groove ball bearings.