Delving into the intricate world of deep groove ball bearing dimensions showcases an intersection of precision engineering and functional versatility. In mechanical contexts, where precision and load management converge, these bearings emerge as a critical component. Their dimensions, intricately calculated to ensure optimal performance, directly impact their efficacy in various applications such as automotive, industrial machinery, and even in the realm of household appliances.
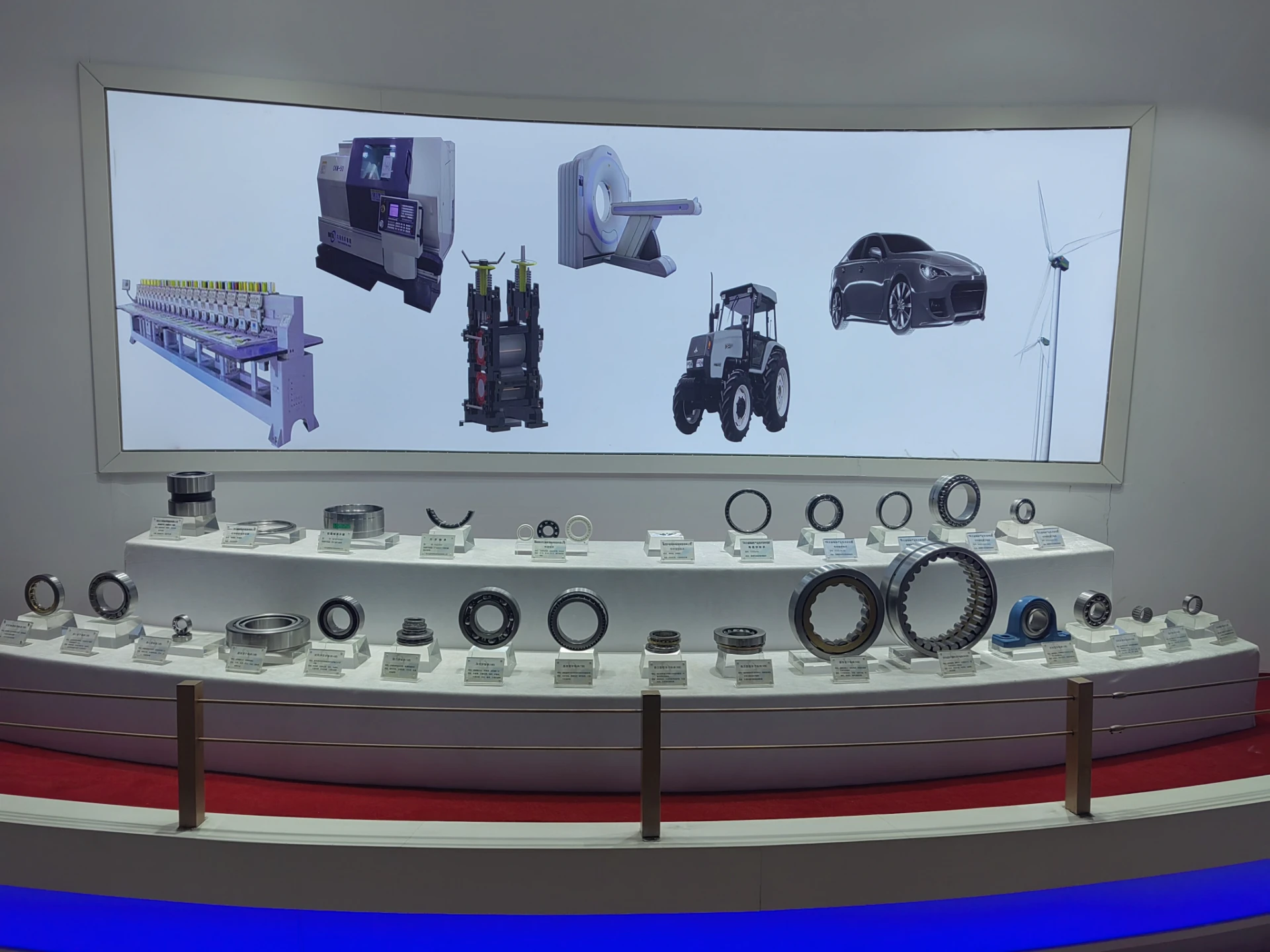
At the heart of understanding deep groove ball bearing dimensions lies the trinity of inner diameter (ID), outer diameter (OD), and width (W). Each of these dimensions plays a crucial role, dictating the functionality and suitability of the bearing for specific applications. Typically, the dimensions follow a standardized system, as prescribed by ISO or ABEC standards, allowing for interchangeability and ensuring global compatibility across different machines and assemblies.
The inner diameter, denoted as ID, serves as the anchoring point for the shaft. The precision of this dimension is paramount; even a slight deviation could lead to improper fitting, causing increased friction and potentially catastrophic system failures. An expertly manufactured ID not only facilitates smooth rotational action but also contributes to the longevity of both the bearing and the associated equipment.
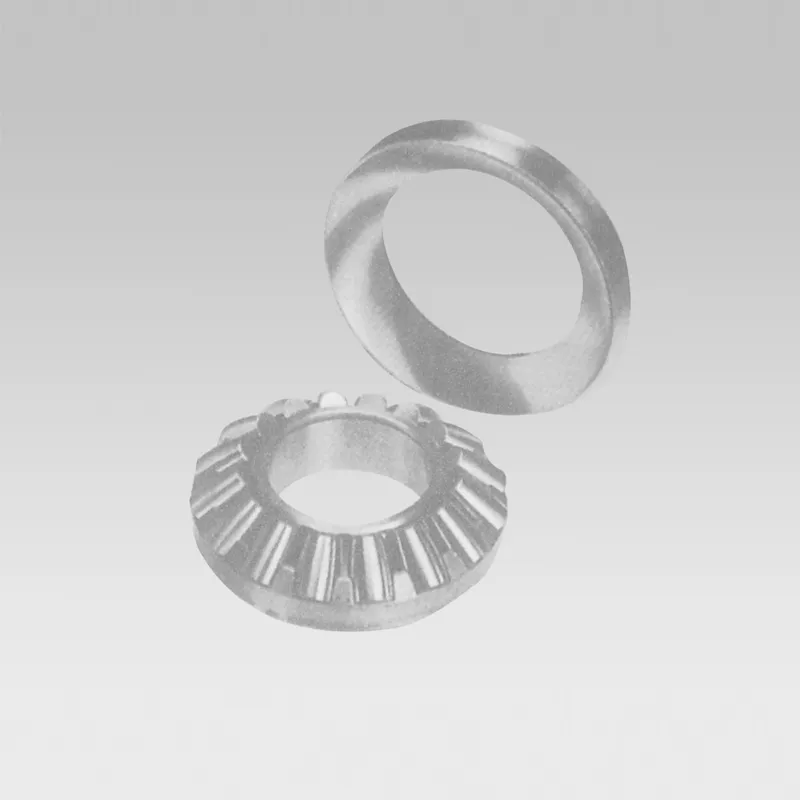
The outer diameter, or OD, is equally critical. It fits into the housing of the machinery or device, securing the bearing in place. The OD ensures that the bearing remains stationary, allowing the inner race and balls to rotate freely and efficiently. Inaccuracies in this dimension could result in displacement or vibration, undermining the equipment's operational integrity.
The width of the bearing, defined as W, provides the bearing with its load-carrying capacity. A broader width accommodates more balls or rollers, distributing the load more effectively and enhancing the bearing’s ability to manage both radial and axial loads. This dimension is crucial when bearings are employed in applications involving significant axial forces or where stability under duress is non-negotiable.
deep groove ball bearing dimensions
Beyond the basic understanding of these dimensions, industry experts must consider the material composition and finish quality. Stainless steel remains a popular choice, renowned for its durability and resistance to corrosion, crucial in environments prone to moisture or harsh chemicals. Advanced ceramic materials and hybrid designs also offer enhanced performance, boasting lighter weights and the ability to withstand higher temperatures and speeds.
The bearing's dimensions also interplay with the lubricant used. A correctly dimensioned bearing with an appropriate lubrication system reduces friction, preventing wear and tear and promoting efficient heat dissipation. This is where the expertise of lubrication engineers becomes vital, as they select oils or greases that complement the bearing’s dimensional properties.
For professionals involved in the procurement and implementation of these mechanical marvels, understanding these dimensions transcends mere technical acumen. It involves a comprehensive appreciation of the bearing's role within the broader mechanical system, aligning its specifications with the intended application's operational demands and environmental conditions.
Moreover, keeping abreast with the latest advancements in bearing technology, such as the introduction of low-noise and energy-efficient options, equips industry leaders with the authority to make informed decisions that balance performance with sustainability. Trust in a supplier's capacity to deliver dimensionally precise and quality-assured bearings further underscores an organization's commitment to operational excellence.
In conclusion, navigating the dimensions of deep groove ball bearings requires a blend of experience and detailed technical knowledge. Professionals must remain cognizant of evolving technological standards and material innovations, ensuring that their choices manifest not only in increased productivity but also in extended equipment lifespan and reliability. As machinery and applications continue to evolve, so too will the exacting standards for these seemingly simple yet fundamentally critical components.