Deep groove ball bearings play an integral role in mechanical applications, offering unmatched efficiency and reliability. Their design caters to various industrial requirements, ensconcing them as an indispensable component in engineering and manufacturing sectors. Unlocking the potential of these bearings begins with understanding their intricate designs and applications.
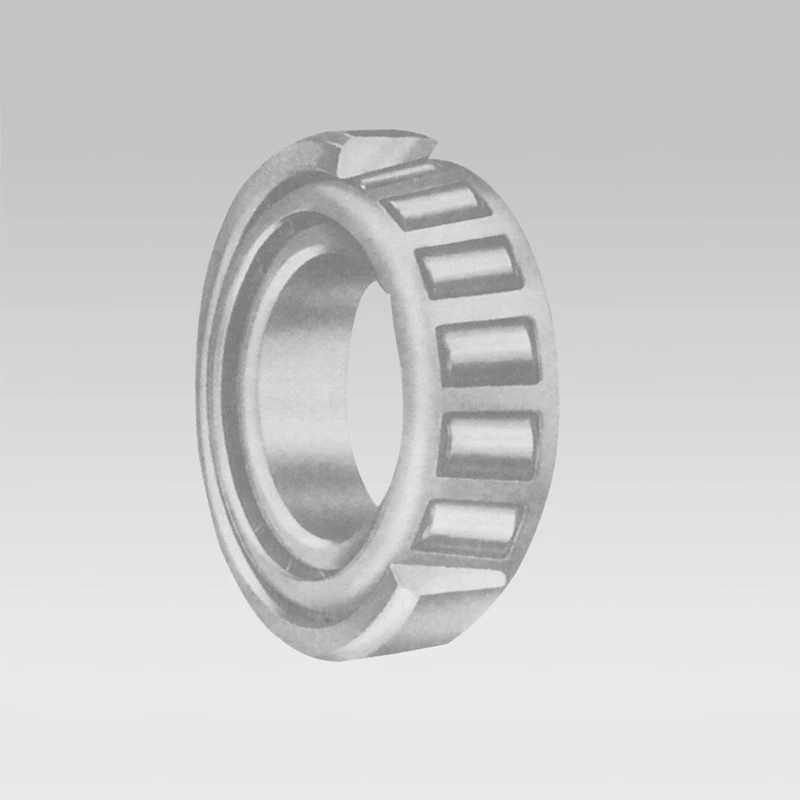
Deep groove ball bearings are renowned for their versatility and practicality. They feature an optimally structured inner and outer ring, which houses several layers of precisely designed balls. These balls articulate around the grooves, providing exceptional rotational efficiency and unmatched load-bearing capabilities. This unique configuration ensures minimal friction during operations, translating into less wear and tear, and significantly extending the lifespan of the machinery where they are employed.
Empirical evidence from industrial applications confirms the robustness and utility of deep groove ball bearings. They are acclaimed for their ability to accommodate radial and axial loads efficiently. A real-world application in automotive engineering highlights their pragmatic application; in car manufacturing, these bearings are integral to systems requiring high-speed rotation and precision, such as in gearboxes and engines. Their capability to manage high-speed rotations without premature failure underscores their reliability.
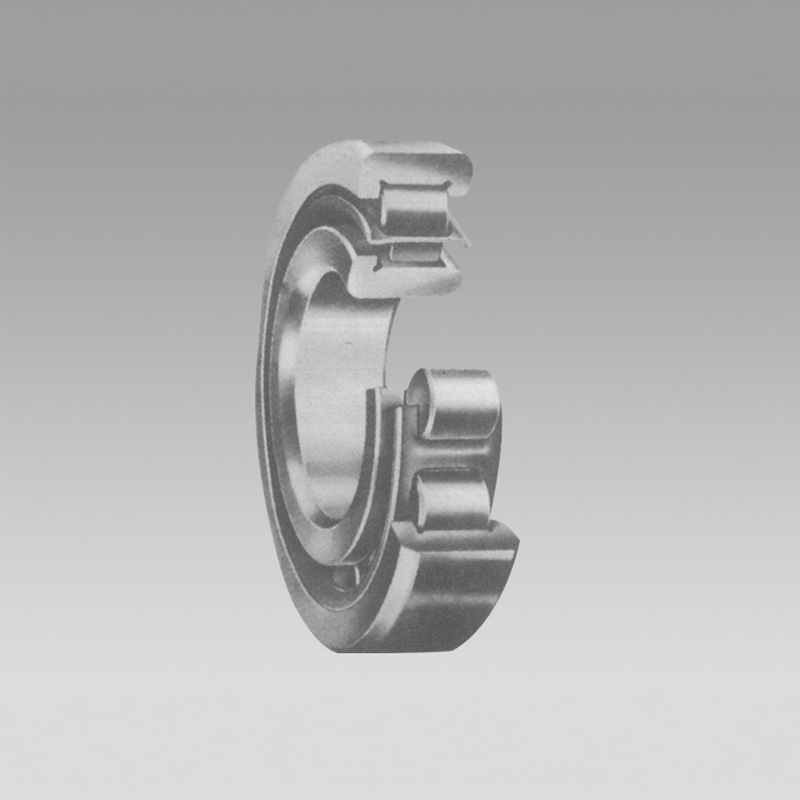
When selecting deep groove ball bearings, several critical factors come into play. The choice should hinge on parameters such as load capacity, operational speed, and the specific environmental conditions of the intended application. Engaging with manufacturers that have a proven track record of producing high-quality bearings is vital. Established manufacturers understand the nuances of bearing design and offer products that meet stringent quality standards.
deep groove ball bearing drawing
Beyond their conventional uses, advancements in technology have spurred the innovation of specialized deep groove ball bearings aimed at niche applications. Innovations such as ceramic-coated bearings have emerged, offering enhanced resistance to high temperatures and corrosive environments. This evolution not only showcases the adaptability of deep groove ball bearings but also solidifies their relevance in modern industrial applications.
Authoritativeness in the domain of deep groove ball bearings is often attributed to an expert's familiarity with both the technical specifications and real-world applications. Technical whitepapers, case studies, and peer-reviewed journals should be critical references for anyone interested in these bearings. These resources provide in-depth analyses and data-driven insights which detail not only the mechanical advantages but also the potential pitfalls and maintenance requirements.
Trustworthiness and credibility in the manufacturing and distribution of deep groove ball bearings are non-negotiable. When sourcing these components, it's crucial to vet suppliers rigorously. Opt for vendors who meet international quality standards such as ISO certifications. Additionally, customer reviews and industry reputation serve as trusted indicators of a supplier's reliability.
Ultimately, the engineering marvel that is the deep groove ball bearing continues to power industries around the globe. Their sophisticated design, coupled with exceptional performance metrics, validates their extensive application from automotive to aerospace industries. As technology evolves, so do these bearings, and staying informed about these advancements ensures that stakeholders can leverage their full potential, driving progress and innovation in various engineering endeavors.