Deep groove ball bearings are fundamental components in various mechanical applications due to their versatility and ability to handle both radial and axial loads. However, their performance can be significantly compromised by misalignment—a common issue that can lead to premature failure, increased wear, and noise.
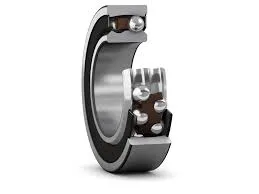
Misalignment typically arises when there is an angular discrepancy between the inner and outer rings of a bearing. This could result from improper installation, shaft deflection, or housing deformation. The consequences of such misalignments are often underestimated until they lead to costly downtime and repairs.
Understanding the subtle signs of misalignment is crucial for maintaining the efficiency and longevity of deep groove ball bearings. One early indicator is an unusual increase in vibration or noise during operation. These noises usually stem from increased friction and can occur due to the irregular contact between the balls and raceways.

Advanced diagnostic techniques have been developed to identify misalignment issues. The use of vibration analysis tools, complemented by infrared thermography, allows for the detection of abnormal heat patterns. These tools are essential for proactive maintenance, enabling technicians to identify issues before they escalate.
Selecting the right bearing is paramount in preventing misalignment. Engineers and procurement specialists should consider designs that allow for a degree of flexibility without compromising on performance. For instance, certain brands offer self-aligning ball bearings that compensate for minor misalignments, reducing the risk of bearing failure in demanding applications.
Incorporating precision-engineered housings can also play a significant role in mitigating misalignment. Properly installed housings ensure that the bearings are aligned correctly with the shaft, minimizing the risk of skewing. The use of machine-grade locknuts and precise mounting procedures can also enhance alignment accuracy.
deep groove ball bearing misalignment
Regular maintenance checks are essential for detecting and rectifying misalignment issues early. This includes inspecting the condition of adjacent components, as damaged or worn-out parts can lead to misalignment. Lubrication practices also influence the performance of deep groove ball bearings. Inconsistent lubrication can cause uneven load zones, resulting in increased friction and wear.
Training and skill development for maintenance staff can vastly improve the reliability of bearing installations. Workshops focusing on best practices for installation, alignment, and maintenance tailor the staff's approach to handling misalignment issues more effectively. Continued education in the latest diagnostic and rectification techniques also promotes an informed maintenance routine.
Collaboration with bearing manufacturers can provide direct benefits. Many companies offer analytical services and training to help businesses optimize the performance of their components. Engaging with these experts can yield insights into specific issues affecting performance, including misalignment, and guide strategic decisions to rectify them.
Emerging technologies present promising solutions for addressing deep groove ball bearing misalignment. The integration of IoT-enabled sensors allows for real-time monitoring and alerts regarding positional errors and temperature fluctuations. Such data-driven insights enable immediate corrective actions, significantly reducing the maintenance lag and ensuring continuous operational efficiency.
In summary, addressing misalignment in deep groove ball bearings involves a multifaceted approach combining precise engineering, regular maintenance, educational initiatives, and advanced technological tools. Recognizing the signs of misalignment early, selecting appropriate bearings, and implementing a robust maintenance strategy can vastly reduce operational disruptions, ensuring prolonged bearing life and optimal performance.