Deep groove ball bearings stand as one of the most versatile and widely used bearings in various applications. Known for their simple design, durability, and capability to handle radial and axial loads, these bearings remain a staple in industries ranging from automotive to aerospace. With many options available in terms of sizes, materials, and specifications, understanding the deep groove ball bearing size chart is essential for both first-time buyers and seasoned engineers.
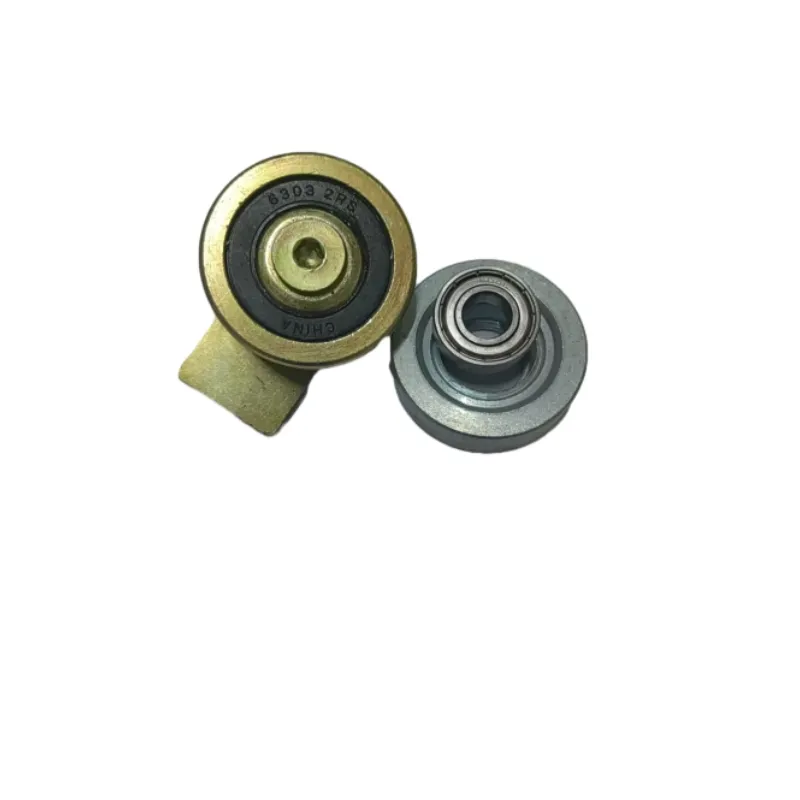
A deep groove ball bearing size chart serves as an indispensable tool in selecting the appropriate bearing for your application. The chart typically showcases dimensions like the inner diameter, outer diameter, and width of the bearings. Most reputable manufacturers provide comprehensive size charts that cover a wide range of standard sizes, and it's essential to align these specs with the unique requirements of your machinery or product design.
The inner diameter (ID) of a deep groove ball bearing is crucial as it must fit snugly on the shaft around which the bearing will pivot. This measurement is particularly important in applications where precision and minimal play are critical, such as high-speed motors or precision instruments. The outer diameter (OD) is equally significant, dictating the space required for the bearing within the machinery. This dimension ensures proper fit into the housing, impacting the overall stability and performance of the machine. Meanwhile, the width of the bearing often correlates with its load capacity, a critical factor when considering the operational demands and lifespan of the bearing under specific conditions.
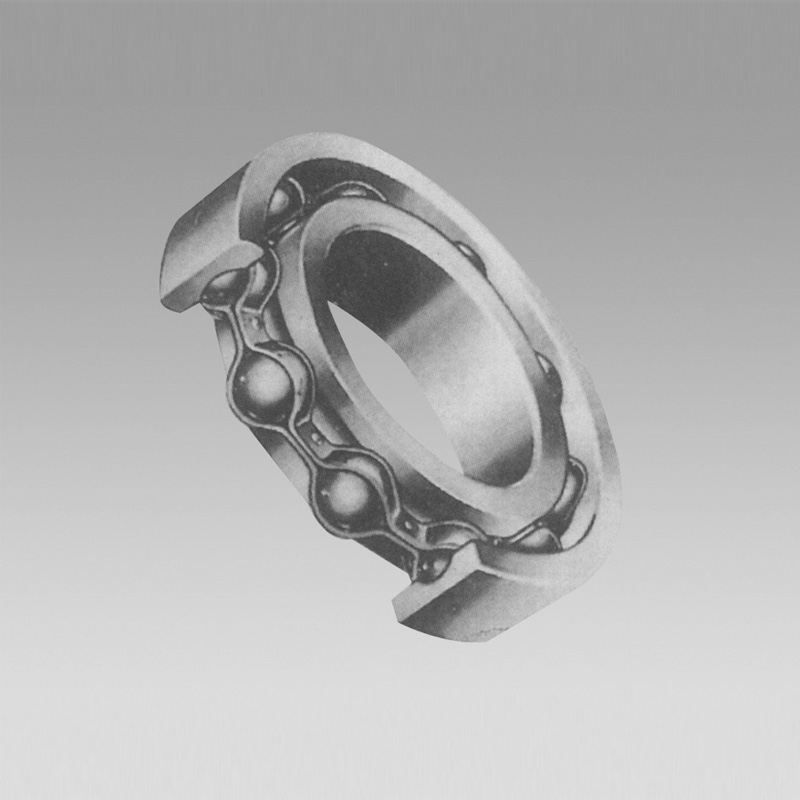
When navigating the deep groove ball bearing size chart, one must also consider material composition and bearing types. Although most deep groove ball bearings are made of stainless steel due to its corrosion resistance and strength, variations exist, such as ceramic or hybrid bearings that offer unique benefits like reduced weight or higher temperature resistance. Catalogues often detail these material benefits, helping professionals make informed choices based on environmental conditions and operational demands.
Selecting the right deep groove ball bearing requires more than just matching sizes; it's about understanding your application’s demands and anticipating future needs. For example, in industries subjected to extreme heat or corrosive chemicals, choosing a bearing with a protective coating or a different material altogether might be necessary. Consultation with engineers or advisors from the bearing manufacturer can provide insights into the best options for challenging applications, thereby ensuring reliability and longevity.
deep groove ball bearing size chart
Accuracy in understanding and applying the information from a deep groove ball bearing size chart can mitigate risks associated with equipment downtime. Underestimating the importance of precise fit and material selection can lead to premature bearing failure, costly repairs, and system inefficiencies. Therefore, users must be meticulous in interpreting size charts and aligning specifications with their equipment needs.
Industry-specific standards such as those from the International Organization for Standardization (ISO) or the American National Standards Institute (ANSI) can also influence bearing selection. These standards provide guidelines on bearing dimensions, load ratings, and test requirements, offering a layer of confidence and trust in the selected components’ performance.
As technology evolves, so do the tools and resources available to users aiming to select the best possible bearing solution. Digital tools, virtual consultations, and advanced software can now aid in simulating bearing performance under various operational conditions, helping users visualize and anticipate any potential issues before installation.
In conclusion, while a deep groove ball bearing size chart is an essential starting point in selecting the right bearing, understanding the nuances of material choice, load capacity, and additional environmental factors can significantly influence equipment performance. Leveraging the expertise offered by manufacturers and aligning choices with established standards ensures the right bearing is chosen for the right application, ultimately strengthening the machine's efficiency and reliability.