Navigating the world of bearings can be daunting for both novices and seasoned professionals.
Among the most popular and versatile types are deep groove ball bearings and angular contact bearings. Each design offers unique features that cater to varying industrial needs and applications, making an informed choice paramount for optimal performance and efficiency.

Deep groove ball bearings are renowned for their simple design and high-speed capabilities. They typically consist of an inner and outer ring, along with a host of rolling elements, and a cage that separates them. Due to their construction, these bearings can handle radial loads and moderate axial loads in both directions. The deep grooves accommodate misalignments and offer low friction, resulting in minimal energy consumption. This efficiency makes them suitable for a diverse range of applications, from household appliances to highly demanding automotive and industrial machinery.
One of the standout features of deep groove ball bearings is their versatility in high-speed applications. The low noise and vibration levels contribute significantly to their reliability, particularly in precision devices such as medical equipment and small electric motors. They are also easy to install and maintain, a crucial factor for operations aiming to minimize downtime and reduce maintenance costs.
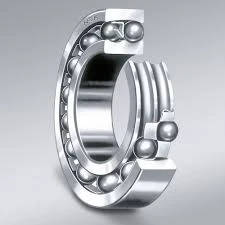
Angular contact bearings, meanwhile, are designed to handle higher axial loads in one direction. Their construction involves angled raceways that create a contact angle from the vertical axis of the bearing. This unique feature enables them to support combined loads and operate at high speeds. This makes angular contact bearings perfect for equipment requiring high levels of accuracy and reliability, such as gearboxes, pumps, and high-speed trains.
deep groove ball bearings or angular contact
An advantage of angular contact bearings is their ability to accommodate thrust loads. Their capacity to manage combined loads is crucial in applications where axial and radial forces act simultaneously. Stacking these bearings back-to-back or face-to-face can further enhance their load management capabilities, offering solutions for intricate applications like precision instruments and aerospace technologies.
To ensure maximum efficiency and lifespan, selecting the right bearing type necessitates a thorough understanding of operational requirements and limitations. One frequently overlooked aspect is the quality and authenticity of the bearing. Inferior or counterfeit products can lead to equipment failure and increased operational costs. Due diligence in supplier selection is critical, ensuring purchases are made from reputable manufacturers known for adhering to industry standards.
Materials and lubrication also play pivotal roles in bearing performance. Modern advancements have seen the introduction of ceramic or hybrid bearings that reduce weight and friction, offering longer lifespans and reduced maintenance. Selecting the appropriate lubricant is equally vital as it minimizes wear and prolongs the bearing's operational capacity. Regular monitoring and maintenance schedules further bolster the longevity and efficacy of the bearings.
In summary, the choice between deep groove ball bearings and angular contact bearings largely depends on the specific requirements of the application at hand. Both offer unique characteristics that cater to different operational needs. Understanding their distinct functions, advantages, and application areas empowers businesses to make informed decisions, ultimately enhancing productivity and reducing downtime. A continued commitment to quality—whether through reputable suppliers, proper materials, or consistent maintenance—ensures reliable performance and maximizes the potential of these critical components.