Deep groove ball bearings are integral components in numerous mechanical applications, revered for their efficiency and reliability. These versatile bearings are utilized globally across a diverse array of industries, from automotive to marine, aerospace to medical equipment, underscoring their adaptability and pivotal role in enhancing operational efficiency.
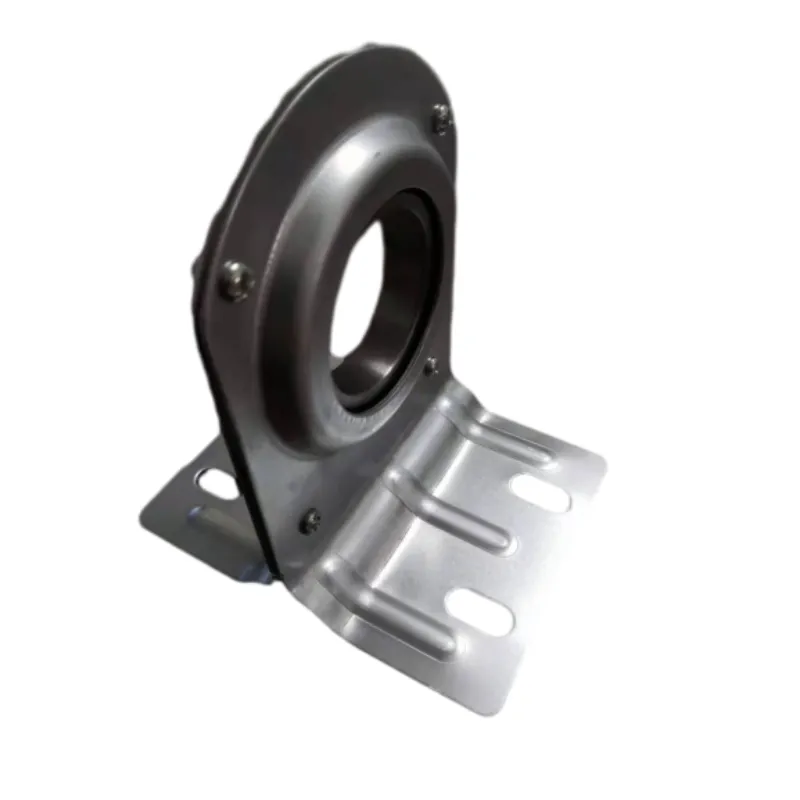
The hallmark of deep groove ball bearings is their simple yet robust design. Comprising an outer ring, an inner ring, a series of steel balls, and a cage to contain and maintain ball spacing, these bearings can handle both radial and axial loads. This versatility is particularly advantageous in machinery where fluctuating forces are prevalent. Their ability to manage dynamic loads while maintaining rotational efficiency makes them indispensable in high-speed applications.
In the automotive industry, deep groove ball bearings are employed extensively in wheels, transmissions, and engines to reduce friction and wear, thereby extending the service life of these components. Their low maintenance requirement further adds value, as they often operate smoothly without needing frequent inspections or lubrication under normal conditions. This trait notably enhances the reliability of vehicles, translating to improved safety and performance on the road.
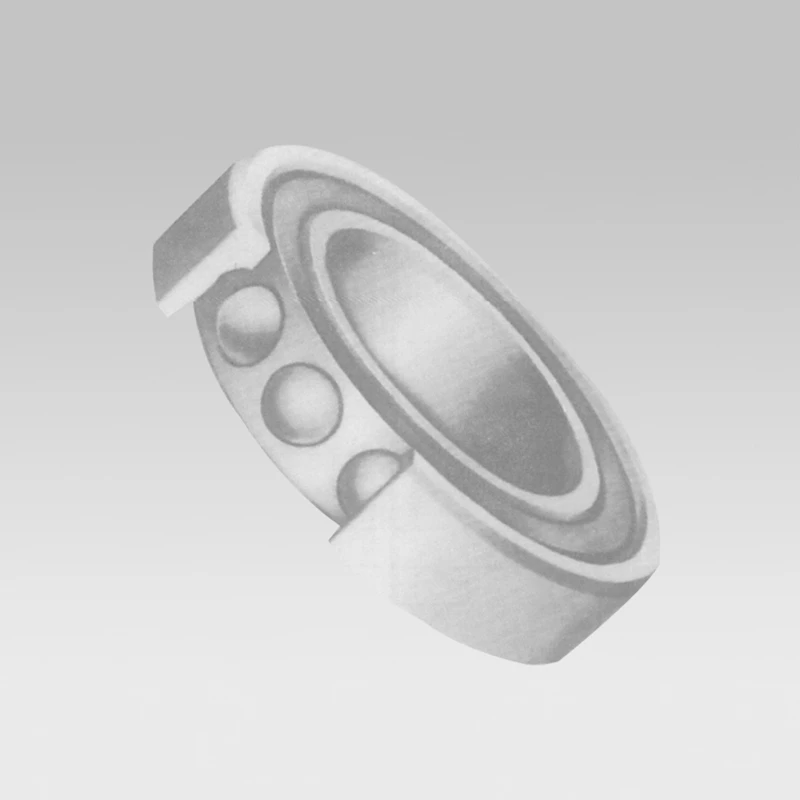
Aircraft manufacturers favor deep groove ball bearings for their lightweight and durable nature, crucial characteristics for flight efficiency and safety. Used in critical areas such as landing gear, wing systems, and avionics, these bearings contribute to the overall integrity and performance of an aircraft. The aerospace sector's stringent quality control and reliability standards highlight the trust placed in these components.
In the realm of consumer electronics, deep groove ball bearings play a significant role in ensuring the quiet, smooth operation of devices such as laptops, vacuum cleaners, and small kitchen appliances. Their ability to support high-speed rotations with minimal noise makes them ideal for these applications, where consumer satisfaction is closely tied to the quietude and smooth functionality of the product.
deep groove ball bearing uses
Apart from their mechanical efficiency, these bearings are essential for eco-conscious operations. The reduced friction facilitated by deep groove ball bearings leads to energy conservation, an increasingly critical consideration as industries pivot towards sustainable practices. By optimizing energy consumption, these bearings support decreased carbon footprints, aligning with broader environmental objectives.
The medical sector also benefits from the use of deep groove ball bearings, particularly in imaging equipment and surgical tools, where precision and reliability are paramount. Ensuring smooth operation in such sensitive instruments is crucial for accurate diagnostics and patient safety, thus emphasizing the trust healthcare professionals place in these components.
In the industrial sector, machinery equipped with deep groove ball bearings often experiences reduced downtime due to the lower maintenance requirements and the bearings' resilience against harsh environments. This characteristic is crucial in manufacturing settings where equipment reliability directly impacts productivity and profitability.
Ultimately, the wide-ranging applications of deep groove ball bearings highlight their unparalleled combination of durability, efficiency, and functionality. Their continuing evolution, with advancements in coatings and materials, promises even greater performance and reliability, further solidifying their role as an indispensable component across various fields. Users ranging from industrial engineers to automotive designers and medical device manufacturers recognize the profound impact that these components have on the effectiveness and dependability of their products.
In summary, the application of deep groove ball bearings is a testament to their importance in facilitating smooth, efficient, and sustainable operations across myriad industries. Their adaptability and reliable performance continue to drive innovations, fueling advancements and setting benchmarks for quality and excellence in mechanical design.