Deep groove bearings stand at the pinnacle of precision mechanics, offering unparalleled performance in an array of applications, from the bustling sectors of automotive engineering to the intricate systems of industrial machinery. These bearings are celebrated not only for their robustness but for their impeccable efficiency in minimizing friction. This expertise translates into an extended lifespan for machinery, reducing operational burdens and maintenance costs, thus driving an evolution within mechanical designs.
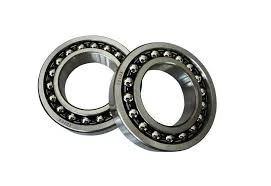
The fundamental construction of deep groove bearings—precision-machined inner and outer rings with a series of polished balls separated by a cage—allows them to handle radial loads and moderate axial loads adeptly. This inherent capability makes them versatile, adapting seamlessly to high-speed applications. An added value is their reduced contact surface, which minimizes friction and subsequently thermal build-up, escalating their durability under continuous strain.
Customers seeking reliable deep groove bearings should prioritize products from manufacturers with authoritative reputations. These manufacturers adhere to stringent industry standards, ensuring quality and consistency across production. Trustworthy companies often employ state-of-the-art technology in their manufacturing processes, including advanced heat treatment methods and high-precision CNC machinery, ensuring each bearing exceeds performance expectations.
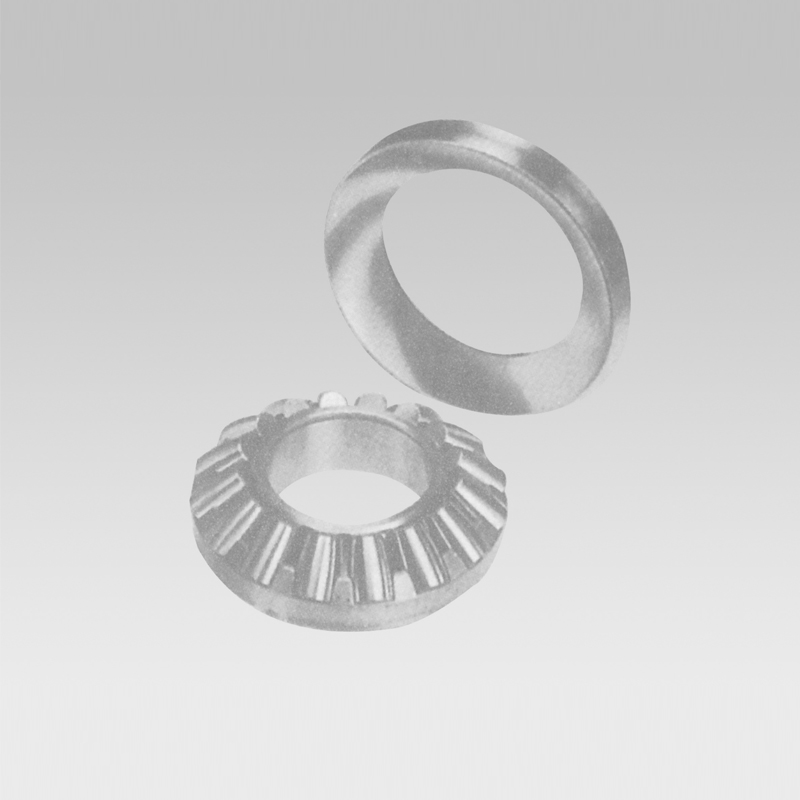
Real-world experiences reflect the deep groove bearing's superiority in diverse settings. For instance, within the automotive industry, their application spans from wheel hubs to transmission systems, significantly improving vehicle performance by bolstering reliability and smoothness. In household appliances, they contribute to noise reduction and energy efficiency, enhancing the user experience. Industrial machines, equipped with these bearings, benefit from reduced energy consumption and minimized downtime due to fewer maintenance interruptions.
The expertise embedded in designing deep groove bearings is a reason behind their ubiquitous presence in modern engineering. Their ability to function under extreme conditions—whether it be temperature fluctuations or high-pressure environments—demonstrates an engineering prowess that combines scientific innovation with practical necessity. Furthermore, their adaptability to various lubrication options, including grease-packed solutions for sealed bearings, extends their usability while ensuring consistent performance.
deep groove bearing
Authoritativeness in the domain of deep groove bearings can be measured by an organization’s continuous commitment to research and development.
Leading manufacturers often collaborate with academic institutions and industry experts to innovate and enhance bearing technologies. This synergy results in breakthroughs such as improved ceramic bearing balls and hybrid models that exhibit even lower friction coefficients and greater resilience.
Trustworthiness is further established through transparent communication about product specifications and adherence to international certifications like ISO and AFBMA standards. This transparency is critical for clients who require assurance that their products will meet specific applications needs without unforeseen complications.
Selecting the optimal deep groove bearing relies on a nuanced understanding of each application's demands, alongside expert consultation. Engineers and procurement specialists must consider dimensions, load capacities, speed ratings, and environmental conditions to ensure the bearing chosen provides the maximum economic and performance advantage.
In conclusion, deep groove bearings encapsulate a convergence of experiential knowledge, technical skill, authoritative manufacturing, and trustworthy practices. They are not merely components but pivotal elements in the operational success of machines and vehicles worldwide. For those seeking to enhance their machinery's performance, deep groove bearings offer an unrivaled solution, promising longevity, efficiency, and reliability in every rotation.