Deep groove ball bearings, a cornerstone in the world of mechanical components, are renowned for their versatility and reliability. These bearings are particularly noteworthy when it comes to handling axial loads, a dimension of force that acts parallel to the bearing shaft. Understanding their capabilities and limitations in this context is crucial for engineers and businesses seeking to optimize machinery performance.
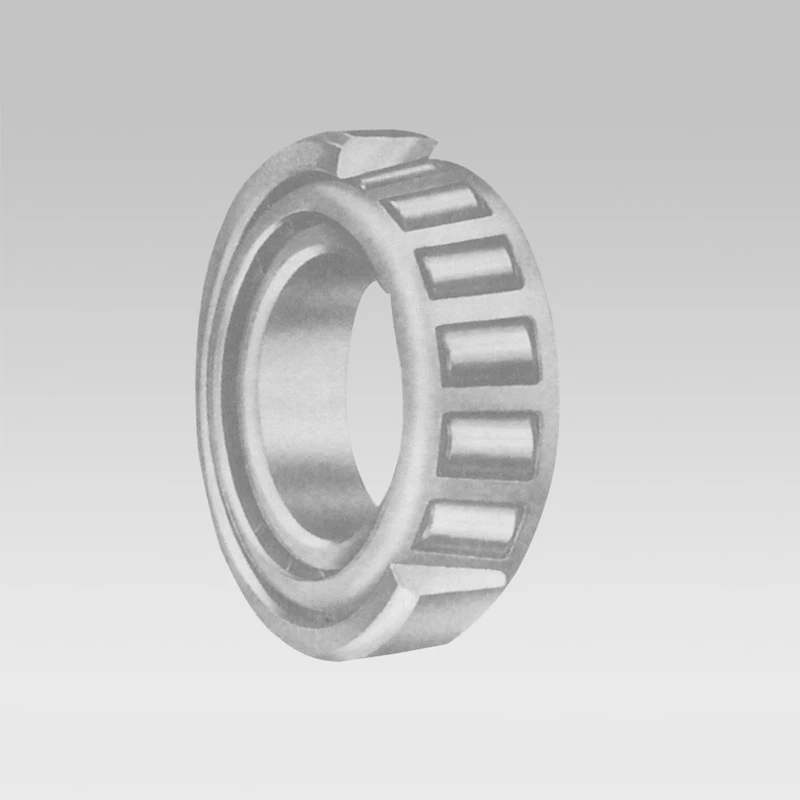
When it comes to axial loads,
deep groove ball bearings offer a unique advantage. With their straightforward design and ability to handle both radial and axial loads, they serve as a highly efficient solution in various applications. The inner and outer rings of these bearings, along with the cage holding the balls, are meticulously engineered to accommodate significant axial forces without compromising on rotational speed or performance.
In real-world applications, deep groove ball bearings are commonly employed in electric motors, automotive transmissions, and industrial equipment. Their ability to sustain modest axial loads makes them suitable for environments where axial forces are common but not excessive. For instance, in an electric motor, axial loads may arise due to thermal expansion or misalignment, and using deep groove ball bearings ensures that these forces are managed effectively, thereby extending the motor's lifespan.
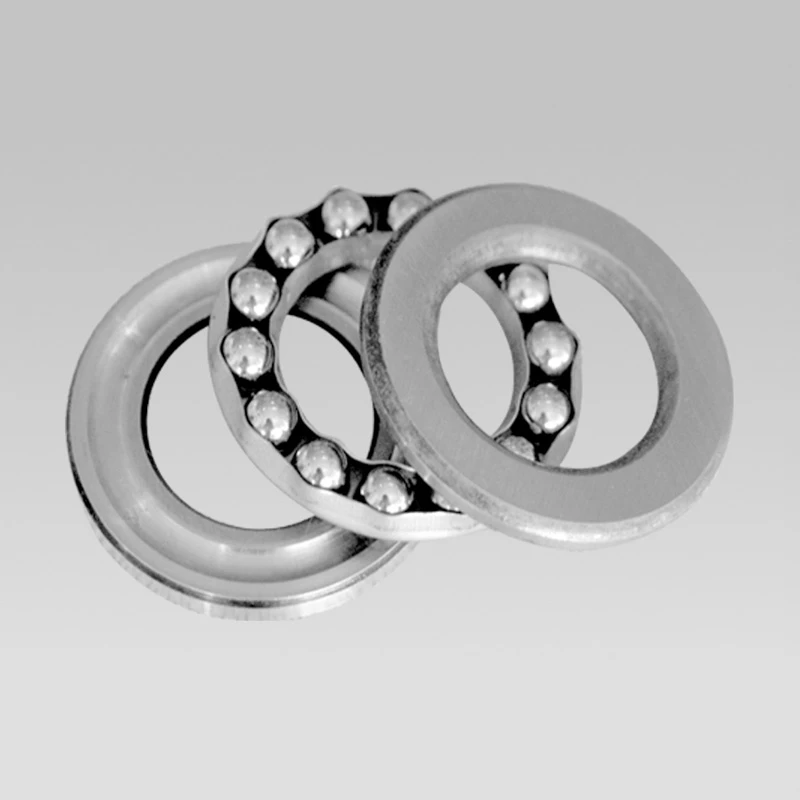
From an expertise standpoint, selecting the right deep groove ball bearing involves careful consideration of load ratings, speed capabilities, and environmental factors. The bearings are typically available in various sizes to accommodate different shaft dimensions and load capacities. Engineers must also take into account the material composition, as bearings made from high-grade steel or ceramic can offer enhanced performance in demanding settings.
deep groove bearing axial load
A critical factor to consider is the axial load-carrying capacity of the deep groove ball bearing. While these bearings are not specifically designed for high axial loads, they can accommodate them efficiently up to a certain limit, often specified by the manufacturer. Exceeding this limit can lead to premature bearing failure, characterized by increased noise, vibration, and eventually, operational breakdown.
One of the authoritative insights in the field is the importance of lubrication and maintenance in extending the service life of deep groove ball bearings under axial loads. Proper lubrication minimizes friction and wear, ensuring smooth operation and reducing the risk of bearing seizure. Regular maintenance checks can also preemptively address any potential issues, such as misalignment or contamination, that may exacerbate the effects of axial forces.
Trustworthiness in utilizing deep groove ball bearings for axial loads is built on sourcing components from reputable manufacturers who adhere to stringent quality standards. These manufacturers typically provide comprehensive data sheets outlining the load ratings, speed capabilities, and recommended operating conditions of their bearings. Such transparency is vital, allowing engineers to make informed decisions and ensure reliable performance in their specific applications.
In conclusion, deep groove ball bearings stand out as a reliable choice for applications involving axial loads, thanks to their design simplicity and capacity to handle combined loads. However, optimizing their performance requires a nuanced understanding of their specifications and rigorous adherence to maintenance protocols. By leveraging expert insights and authoritative knowledge, businesses can harness the full potential of these bearings, ensuring operational excellence and longevity in their mechanical systems.