Flange deep groove ball bearings are a crucial component in countless machinery applications, particularly where space and weight considerations are paramount. These bearings provide essential support for axial and radial loads, while their flanged design offers added stability and ease of installation. This article explores the practical uses, benefits, installation tips, and maintenance strategies for these essential components, drawing from industry expertise and real-world experiences.

Flange deep groove ball bearings are renowned for their versatility. They are commonly used in industries ranging from automotive to industrial machines, offering reliable performance in high-speed operations. The flanged edge helps ensure precise alignment in installation processes, reducing the need for additional components and cutting down on assembly time and costs. This advantage is vital in assembly lines where efficiency is crucial to maintaining production timelines.
One key indicator of expertise in using flange deep groove ball bearings is understanding the nuances of material selection. These bearings are often available in various materials like steel, stainless steel, and ceramic. Steel bearings are the most common due to their excellent balance between strength, cost, and availability. High-grade stainless steel bearings are preferable in environments exposed to moisture or corrosive substances due to their enhanced corrosion resistance. For applications demanding extreme precision and minimal friction, ceramic bearings provide a significant advantage with their superior hardness and thermal resistance.
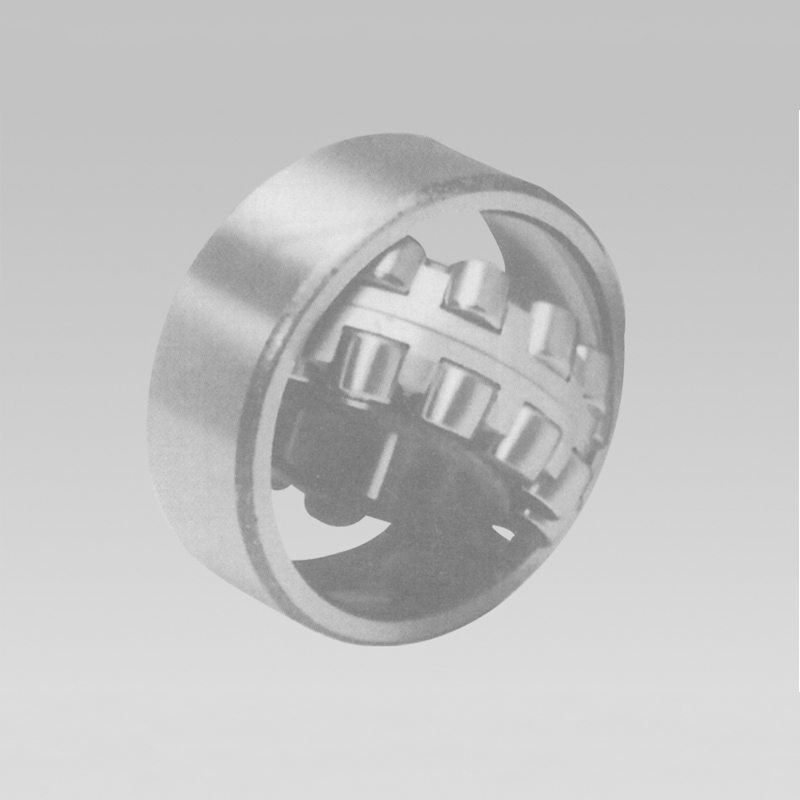
Authoritativeness in the field can be demonstrated by recognizing the nuances of load dynamics and selecting the appropriate bearing type and size. Selecting a bearing with the correct load rating ensures long-lasting performance and avoids premature failure. It's crucial to calculate both the dynamic and static load ratings to determine the suitability of a bearing for a particular application. This calculation often requires consultation with engineering specification sheets or direct contact with manufacturers who can provide detailed load rating charts for their products.
Trustworthiness extends into the installation and maintenance of flange deep groove ball bearings. Proper installation is critical to achieving optimal performance and longevity. Installers should ensure that the shaft and housing are thoroughly cleaned and free from contaminants before fitting the bearing. A slight misalignment could result in uneven load distribution, leading to increased wear and noise during operation. Therefore, precision tools and methods are indispensable during the installation process.
flange deep groove ball bearing
Maintenance is another critical aspect that underscores trust in the use of flange deep groove ball bearings. Regular inspection and lubrication are necessary to sustain peak functionality. Bearings require a compatible lubricant to minimize friction and wear. For industrial applications, industrial-grade greases are typically recommended. Users should adhere to a regular maintenance schedule, checking for signs of wear, noise, or vibration, which might indicate potential issues. A proactive maintenance strategy can significantly extend the service life of these bearings and improve the overall reliability of the machinery in which they are installed.
Real-world experience has shown that companies investing time and effort into understanding and properly implementing flange deep groove ball bearings can significantly reduce downtime. This advantage leads to increased productivity and reduced operational costs, a substantial benefit in highly competitive industries. Furthermore, engaging with experts and professionals in the bearings industry can provide valuable insights into emerging trends and technologies that could further enhance their application and efficiency.
It's worth noting that the integration of flange deep groove ball bearings in modern machinery also aligns with advances in automation and smart technology. As industries move towards smart manufacturing, these bearings are adapting to support sensing and monitoring technologies, contributing to predictive maintenance strategies. By enabling more proactive management of wear and potential failures, machinery can achieve higher levels of uptime and reliability.
In conclusion, mastering the application of flange deep groove ball bearings involves a comprehensive understanding of material selection, load considerations, precise installation, and diligent maintenance practice. Engaging deeply with industry standards and technological advancements ensures these components continue to deliver robust performance and savings across various sectors. Trust in their reliability not only bolsters machine performance but also contributes to operational excellence and sustainable industrial practices.