Understanding the significance of the groove in ball bearings is crucial for engineers and product developers who rely on these components for various applications. Groove design directly influences the bearing's performance and longevity, making it an essential consideration for any project involving rotational motion systems.
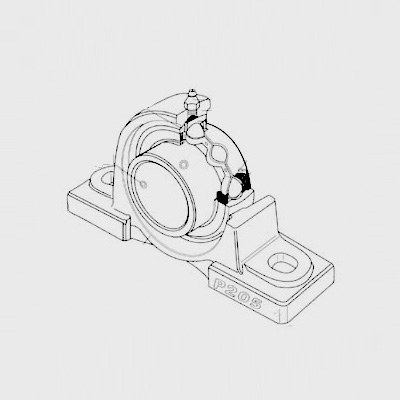
First and foremost, a groove in a ball bearing is the precisely engineered pathway where the balls move. This groove allows for the smooth rotation of the rolling elements, thereby reducing friction and, in turn, heat generation during operation. Its geometry usually takes the form of an arc or a 'raceway'. The design of this raceway is pivotal as it impacts the load-carrying capacity of the bearing. A well-designed groove allows for an even distribution of stress across the balls, reducing the risk of premature failure.
One key aspect of groove design is the groove curvature radius, which should ideally match the radius of the ball bearings. A common recommendation is to have the groove curvature slightly larger than the ball radius, to ensure optimal contact without excessive slippage or misalignment. This precision in matching radii ensures a thin lubrication film is maintained, which is critical for minimizing metal-to-metal contact and thereby extending the bearing's lifespan.
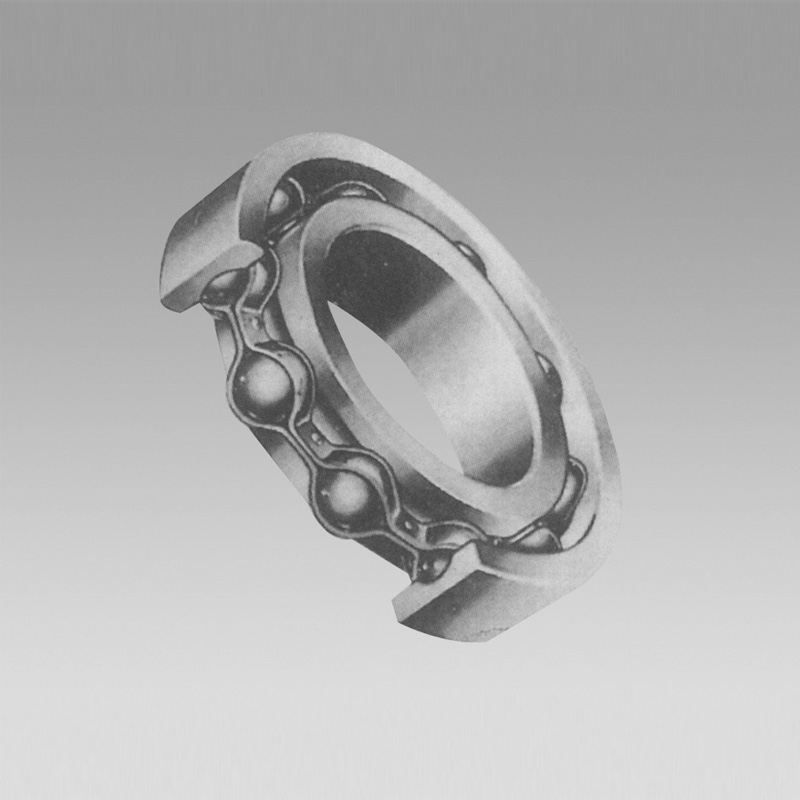
The depth of the groove is another critical factor that demands attention. A shallow groove might promote higher speeds, but if too shallow, it can lead to an increased risk of ball escape during operation. Conversely, a deeper groove might enhance the bearing's ability to handle axial loads but could generate more friction under certain conditions. Achieving the right balance in groove depth based on the load and speed requirements of the application is fundamental for efficient bearing operation.
Different applications may necessitate different groove geometries. For instance, applications demanding high-speed operation often use bearings with a more shallow groove design to minimize the friction generated from smaller contact areas. Meanwhile, heavy-load applications might favor deeper grooves or even angular contact designs to ensure stability and optimal performance under load.
groove for ball bearings
Materials used in groove construction also influence the performance of ball bearings. Steel is typically the material of choice due to its durability and robustness. However, advancements in materials science have introduced ceramics and composite materials, which offer lighter weight and superior temperature performance. Such materials can significantly reduce the bearing's wear and tear, enhancing operational reliability especially in high-speed applications.
Regular maintenance and inspection of the ball bearings’ grooves can help in recognizing early signs of wear and tear. Over time, bearing grooves may exhibit signs of concave wear or spalling, which may degrade performance and efficiency. Utilizing modern techniques such as magnetic resonance imaging and ultrasonic testing can be beneficial for assessing groove condition without disassembly, thereby averting potential operational disruptions.
In the market today, leading manufacturers invest heavily in research and development to innovate groove designs, focusing on improving bearing efficiency, reducing maintenance downtime, and maximizing lifecycle performance. These advancements further reinforce the importance of precision engineering in groove creation, which contributes significantly to the overall trustworthiness and credibility of the bearing product.
Furthermore, aligning groove features with industry standards and certifications helps in ensuring that the product meets the rigorous demands of various applications, ranging from automotive to aerospace technology. By maintaining high manufacturing standards, companies commit to providing reliable and safe products, building their reputations as industry leaders.
As the demand for efficient and high-performing ball bearings continues to grow, understanding the intricacies of groove design remains a critical component of product development. It establishes a foundation of expertise and reliability, guiding engineers in crafting components that excel in durability and functional integrity. Through informed design and attention to detail, the groove in ball bearings will undoubtedly continue to be a cornerstone of mechanical innovation and excellence.