High precision deep groove ball bearings have emerged as pivotal components in modern engineering and manufacturing sectors, celebrated for their unparalleled efficiency and reliability. As industries evolve, the demand for high-quality, exacting components has soared, setting these bearings apart as exceptional solutions for various applications.
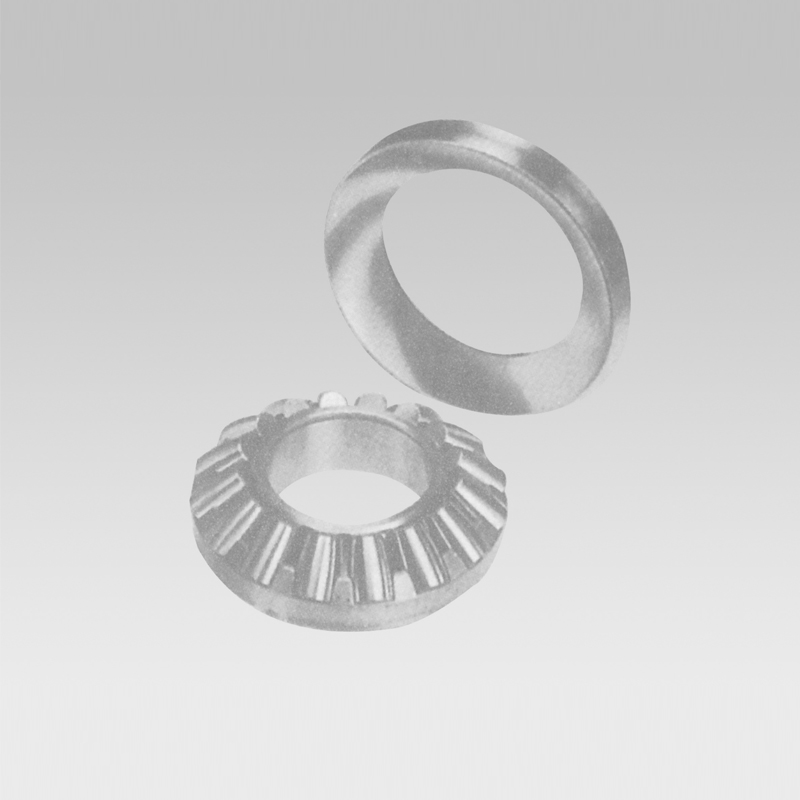
Deep groove ball bearings are renowned for their simple yet robust design, featuring inner and outer rings, a cage, and a series of balls. This simplicity belies their capability to handle radial and axial loads, making them indispensable in scenarios requiring high speed and precision. The specialization in high precision variants underscores an evolution towards precision engineering, where each component’s role is amplified.
The accuracy of these bearings is measured in microns, ensuring the utmost precision in operations where even the slightest deviation can lead to significant inefficiencies. Industries such as aerospace, automotive,
and robotics rely heavily on deep groove ball bearings to maintain operational excellence. In aircraft engines, for instance, where the margin for error is almost non-existent, these bearings ensure smooth, uninterrupted operation, bolstering overall safety and performance.
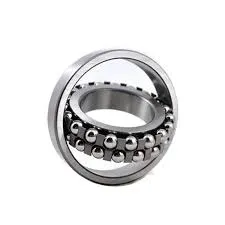
One of the distinguishing features of high precision deep groove ball bearings is their low frictional resistance, which is crucial in applications demanding high-speed rotation. This characteristic not only enhances the mechanical efficiency but also prolongs the lifespan of the machinery, reducing maintenance costs and downtime. Manufacturers employ advanced materials and coatings to achieve this low friction environment, underscoring the expertise involved in their production.
Professional expertise in selecting and implementing these bearings is essential. Engineers and technical experts undergo rigorous training to understand the nuances involved in bearing selection. Factors such as load capacity, temperature tolerances, and environmental conditions are meticulously analyzed to ensure optimal performance. This expertise is a cornerstone of the successful deployment of high precision deep groove ball bearings in critical applications.
high precision deep groove ball bearing
The credibility of manufacturers plays a fundamental role in establishing trustworthiness in this niche. Leading manufacturers are committed to rigorous quality control, adhering to international standards like ISO 9001 to assure clients of their commitment to excellence. Transparency in production processes, coupled with regular audits and certifications, further solidify a manufacturer’s reputation, making them a reliable partner for businesses worldwide.
Feedback and real-world experience from industry professionals further establish the reliability of these bearings. Testimonials and case studies often highlight the tangible benefits, such as reduced operational costs and significant performance boosts, reinforcing their authority in the market. Companies frequently share insights into their experiences, establishing a repository of knowledge that supports informed decision-making for future projects.
Incorporating high precision deep groove ball bearings into operations transcends mere mechanical upgrades. It reflects a strategic decision to embrace high standards of efficiency and reliability. As industries progressively shift towards automation and precision engineering, the role of these bearings becomes increasingly crucial, ensuring that enterprises remain competitive and forward-thinking.
The continuous innovation and development in the field of bearing technology hold promise for even greater advancements. Research and development efforts are consistently aimed at enhancing material science, reducing environmental impact, and increasing load capacities, aligning with the future needs of advanced industries. This commitment to progress reflects an unwavering dedication to meeting the evolving demands of global engineering challenges.
In summation, high precision deep groove ball bearings are not just components; they are integral to the machinery that drives progress across numerous sectors. Their well-documented reliability and efficiency make them indispensable in an era where precision is paramount. The expertise required to manufacture and utilize these bearings effectively ensures that they remain at the forefront of industrial innovation, securing their place as cornerstones of modern engineering excellence.