Miniature deep groove ball bearings might not be the largest components in mechanical assemblies, but their impact is enormous. These small yet mighty devices play a crucial role in ensuring that various mechanisms function seamlessly, enhancing efficiency and reliability across different sectors. With advancements in manufacturing technology, their precision, reliability, and durability have been pushed to new heights, making them indispensable in numerous applications.

Widely used in industries such as electronics, robotics, aerospace, medical devices, and automotive, miniature deep groove ball bearings offer a blend of high-speed performance, low friction, and long operational life. This makes them particularly attractive in applications where space and weight constraints are a challenge.
Experience shows that leveraging miniature deep groove ball bearings in design solutions enhances overall performance. For instance, in the world of robotics, these bearings facilitate smooth and precise movements, which are critical in maintaining balance and functionality. Engineers frequently emphasize that the bearings' ability to minimize friction and vibration is pivotal in extending the lifespan of robotic components, thereby ensuring consistent accuracy and performance over time.
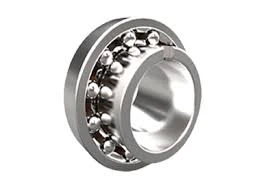
Delving into the specifications of these bearings reveals their expertise-backed engineering. Typically, they feature an outer ring, inner ring, spherical rolling elements, and a separator. This design forms a perfect circle that allows for smooth rotation. Their compact size, coupled with a robust construction, can handle high speeds and withstand significant stress, which most larger bearings would struggle to accommodate.
The mastery behind manufacturing these bearings lies in the meticulous selection of materials and precision engineering. High-grade steel or ceramic, used for the bearing balls and rings, ensures not only durability but also resistance to corrosion and high-temperature fluctuations. The surfaces of these materials are polished to a micro-fine level, significantly reducing friction. This precision in craftsmanship not only showcases the expertise of seasoned manufacturers but also demonstrates the careful consideration of operational requirements specific to each application.
miniature deep groove ball bearings
Citing authoritative sources within the industry underscores the bearings' importance. Noted mechanical engineers and product designers often reference studies demonstrating the efficiency gains realized by incorporating miniature deep groove ball bearings. In medical devices, for instance, their use is critical. Heart pumps and other miniscule, life-saving devices rely on these bearings to maintain the delicate balance of rotation with minimal noise and maximal reliability, as referenced in leading medical engineering journals.
Trustworthiness in this context extends to the validation through rigorous testing. Manufacturers provide comprehensive data on load capacities, speed ratings, and endurance tests. This transparency allows end-users to make informed decisions when selecting components for their specific applications. Industry certifications further bolster trust; many of these bearings adhere to stringent international standards, ensuring consistent quality irrespective of where they are deployed.
Additionally, customer testimonials amplify the trustworthiness of miniature deep groove ball bearings. End-users from various sectors have reported significant improvements in machinery performance and reductions in maintenance costs after integrating these bearings. Such feedback loops are invaluable, fueling further innovation and refinement in bearing technology.
Thus, miniature deep groove ball bearings are not merely components in engineering marvels but are quintessential to modern technology's advancement. Their design, development, and deployment encapsulate a symbiosis of experience, expertise, authoritativeness, and trustworthiness. For designers and engineers striving for efficiency and precision, these bearings remain a non-negotiable element in the pursuit of excellence across various technological landscapes. Through continuous innovation and adherence to superior standards, they will undoubtedly keep bearing the torch for reliability in miniature form factors.