Plastic deep groove ball bearings have emerged as a crucial component in the modern engineering world, offering an innovative alternative to traditional metal bearings. These bearings are engineered for applications that demand lightweight, corrosion-resistant, and cost-effective solutions without compromising on performance. With a growing interest in sustainable and efficient industrial components, plastic deep groove ball bearings are carving out a niche market, thanks to their unique attributes and competitive advantages.
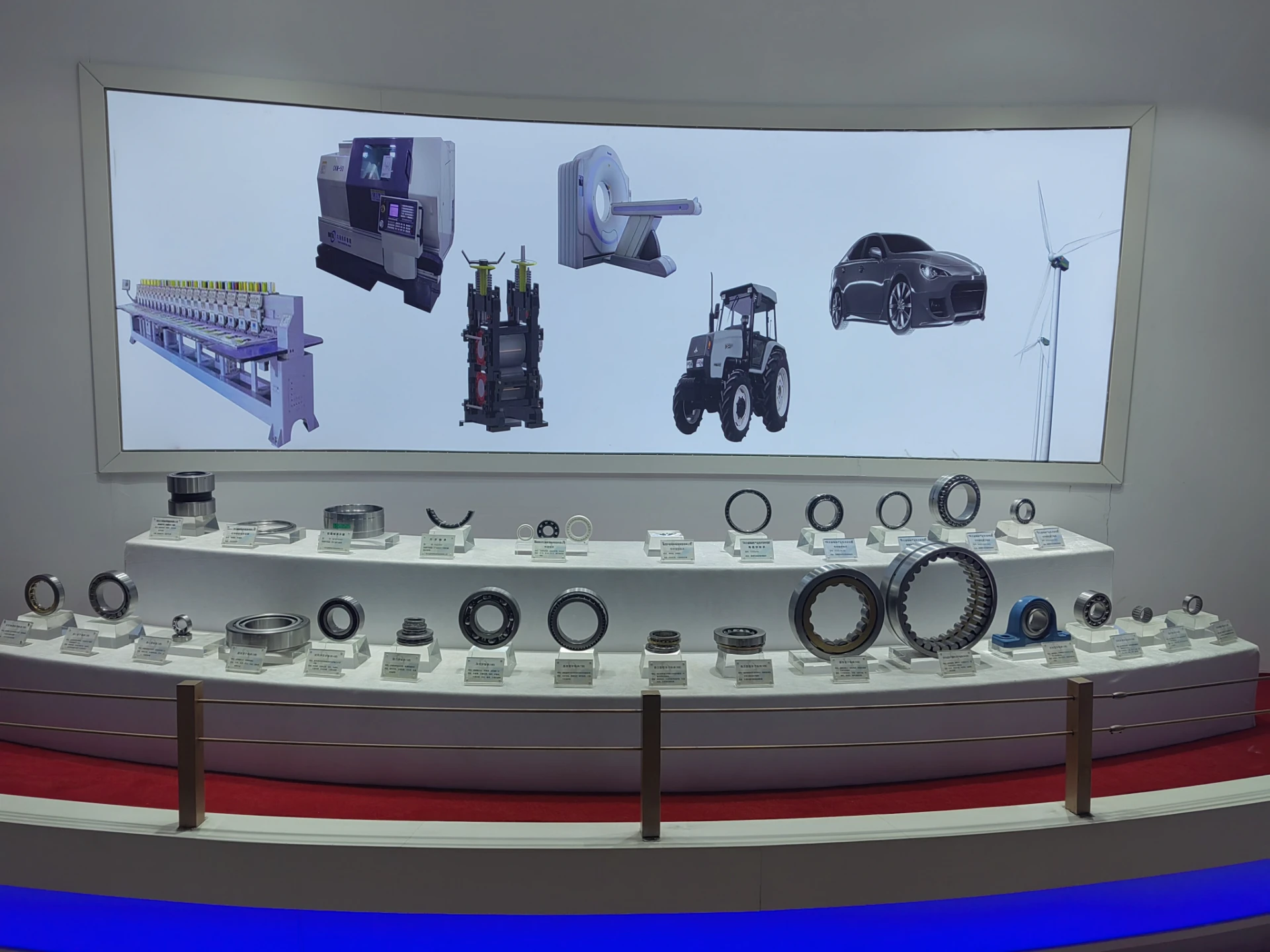
A key feature of plastic deep groove ball bearings is their lightweight nature. Composed of high-performance polymers, these bearings reduce the overall weight of mechanical systems, making them ideal for aerospace, automotive, and robotics applications where minimizing weight is paramount. Additionally, their lightweight nature translates into lower inertia, which improves the efficiency of high-speed operations, ultimately enhancing the longevity and performance of machinery.
Corrosion resistance is another significant benefit. Unlike their metal counterparts, plastic deep groove ball bearings are immune to rust and chemical damage. This makes them especially suited for environments exposed to moisture, chemicals, or extreme temperatures, such as marine applications or food processing industries where hygiene and cleanability are crucial. The absence of metal components further reduces the risk of contamination, thereby aligning with stringent industry standards and regulations on safety and health.
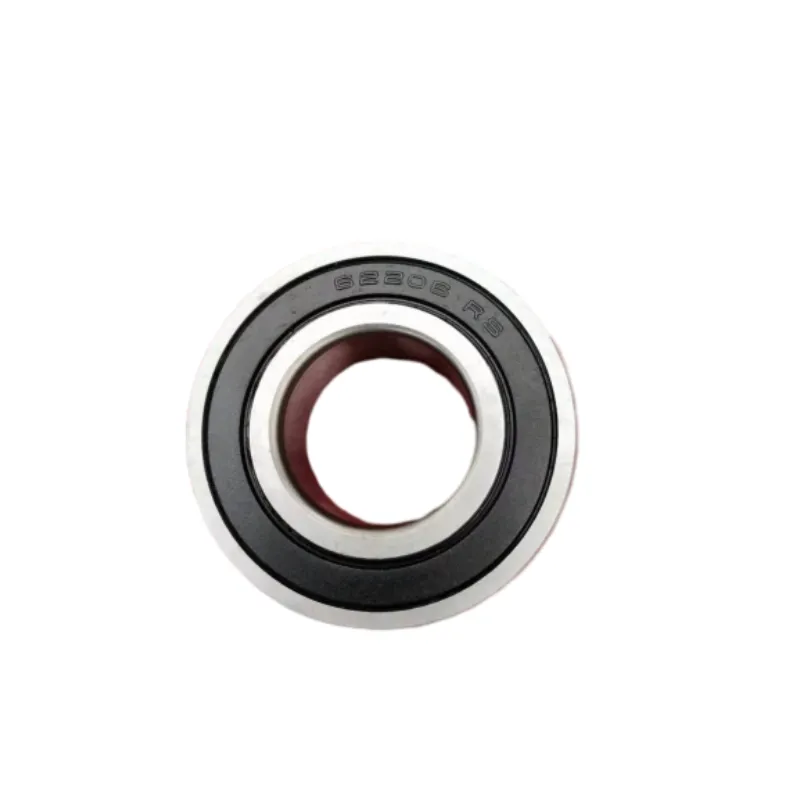
Furthermore, plastic bearings exhibit impressive resistance to wear and friction. Engineered from advanced polymers that can include additives like glass fibers or molybdenum disulfide, these bearings are designed to withstand significant wear while maintaining smooth, noiseless operation. This characteristic is crucial for applications in medical devices or laboratory equipment where any particle shedding could compromise the integrity or reliability of the systems.
From a cost perspective, plastic deep groove ball bearings offer an economical solution. The manufacturing process for plastic components is often less energy-intensive than that for metal parts, leading to reduced material waste and lower production costs. This cost-effectiveness, coupled with their long service life and minimal maintenance requirements, makes them an attractive option for businesses looking to optimize operational budgets without sacrificing quality or performance.
plastic deep groove ball bearings
Technical expertise in materials science and engineering has driven the development of these bearings, ensuring they meet rigorous industry standards. Leading manufacturers employ state-of-the-art techniques such as computer-aided design (CAD) and finite element analysis (FEA) to refine the geometry and material composition of these bearings, enhancing their load-bearing capacity and operational life.
Trust in plastic deep groove ball bearings is continually reinforced by their successful deployment across diverse industries. Case studies and real-world applications consistently demonstrate their ability to outperform traditional bearings in terms of longevity and reliability. Their adoption by leading global enterprises serves as a testimonial to their capabilities and innovative edge in modern engineering solutions.
Importantly, as industries shift towards eco-conscious practices, the environmental benefits of plastic bearings are gaining attention. The ability to recycle plastic components contributes to sustainability goals, and the reduction in energy consumption during manufacturing aligns with green engineering practices. These attributes not only reduce the carbon footprint but also support companies in achieving their sustainability targets.
In conclusion, plastic deep groove ball bearings represent a harmonious blend of innovation and functionality. Their unique properties offer unbeatable advantages in specific applications, redefining expectations in industries that demand precision and efficiency. As technology advances, it is anticipated that the versatility and sustainable profile of these bearings will further cement their status as integral components in the modern industrial landscape.