In the dynamic world of industrial machinery and engineering, deep groove ball bearings are indispensable components. These bearings ensure the smooth operation of many devices, ranging from small-scale gadgets to enormous turbines.
One key factor influencing the performance of deep groove ball bearings is the contact angle. Understanding the intricacies of this parameter can significantly enhance the efficiency and longevity of machinery, ensuring optimal performance and reduced downtime.
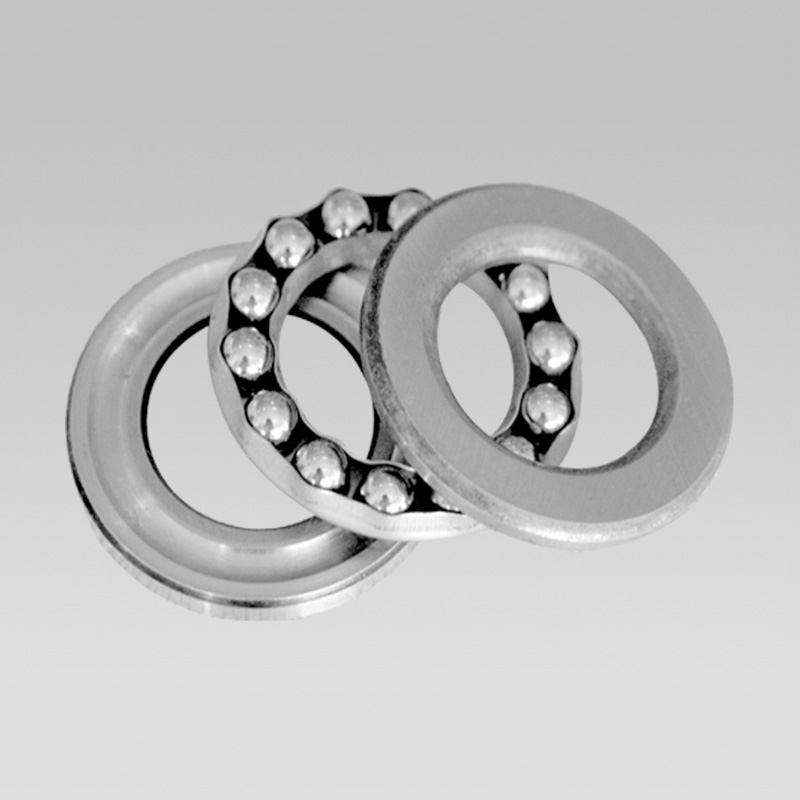
The contact angle in a deep groove ball bearing refers to the angle formed between the bearing's raceway and the contact point of the ball. This angle is crucial as it determines the bearing's ability to handle axial and radial loads. Typically, deep groove ball bearings are known for their ability to support high-speed rotations and moderate radial loads. However, variations in the contact angle can tweak their load-bearing capabilities, influencing both axial and radial support.
Experience underscores the importance of selecting the appropriate contact angle for specific applications. A bearing with a larger contact angle is more suitable for applications where axial loads are prominent. Conversely, a smaller contact angle is preferable for applications with substantial radial load demands. This nuanced understanding can prevent premature wear and tear, thus extending the life of the machinery and ensuring operational stability.
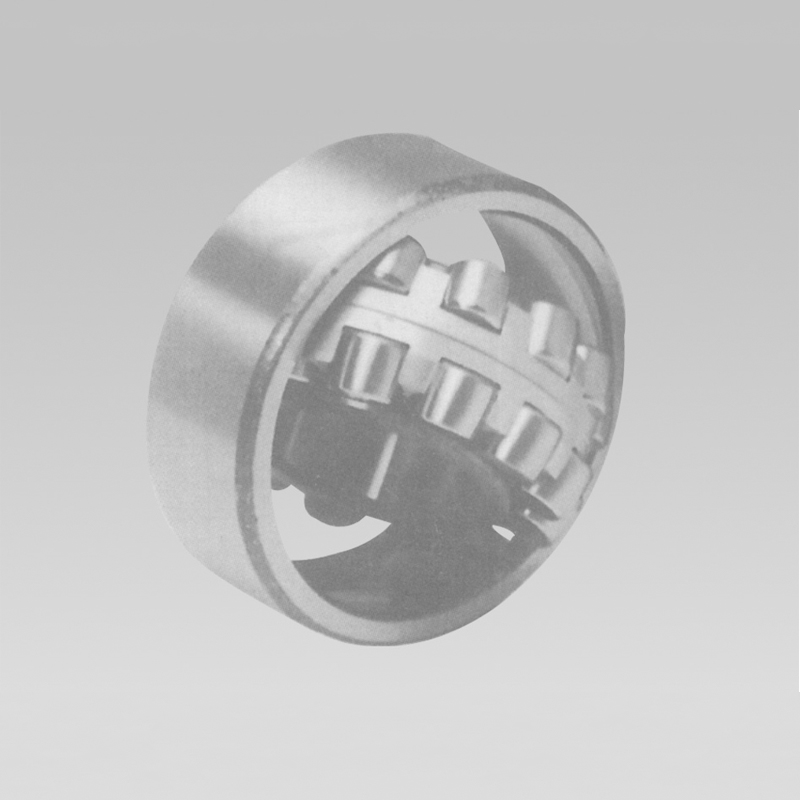
From an expertise standpoint, engineers must leverage precise calculations when determining the optimal contact angle for their specific application. This involves a comprehensive assessment of load dynamics and rotational speed requirements. Advanced software tools and simulation techniques are pivotal in modeling these scenarios, allowing engineers to predict how variations in contact angle will affect overall performance.
deep groove ball bearing contact angle
In the realm of authoritativeness, industry standards such as ISO and ABEC classifications outline guidelines for bearing specifications, including contact angles. Compliance with these standards not only guarantees quality assurance but also reinforces trust amongst clients and stakeholders. Companies must also engage in continuous research and development to innovate and refine contact angle adjustments, ensuring their bearings remain competitive and technologically advanced.
Trustworthiness in the context of deep groove ball bearings is paramount. Manufacturers and suppliers should be transparent about the specifications and capabilities of their products. Providing detailed documentation, including test results and performance data, can bolster confidence in the product's capability to meet specific load demands and environmental conditions. Furthermore, offering robust after-sales support and warranty programs contributes significantly to user trust and satisfaction.
Moreover, real-world case studies showcase the impact of contact angle optimization. For instance, a manufacturing plant experiencing frequent bearing failures conducted a thorough analysis and discovered that the contact angle was not suited for the predominant axial loads encountered in their machinery. By adjusting the contact angle and choosing a bearing tailored to their operational needs, they significantly reduced maintenance costs and enhanced production uptime.
In conclusion, the contact angle in deep groove ball bearings is a decisive factor that can make or break the efficiency of machinery. Through a harmonious blend of experience, professional expertise, adherence to authoritative standards, and a commitment to trustworthiness, organizations can ensure that they select and utilize the most suitable bearings for their applications. Such an approach not only elevates machine performance but also bolsters the reputation and reliability of both product and provider, yielding long-term industrial success and client satisfaction.