Deep groove ball bearings are indispensable components in a wide range of machinery and mechanical setups. Their reliability and versatility make them a preferred choice, but calculating the load they can handle is a critical consideration. Often overlooked, understanding the load capacity can significantly improve performance, longevity, and safety.
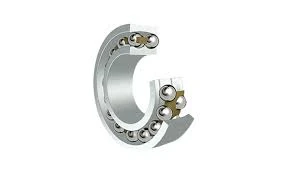
When it comes to deep groove ball bearing load calculation, thorough analysis and comprehension are essential. These bearings support radial loads and can also handle moderate axial loads. Because of their simple design, they are easy to use and maintain, making them suitable for high-speed applications.
Calculating the bearing load involves several steps. First, it is vital to understand the types of loads that the bearings will encounter. This includes radial loads, axial loads, and combined loads. Radial loads act perpendicular to the shaft, while axial loads occur parallel to the shaft. Deep groove ball bearings are primarily designed to handle radial loads but can accommodate some axial loads depending on the internal design.
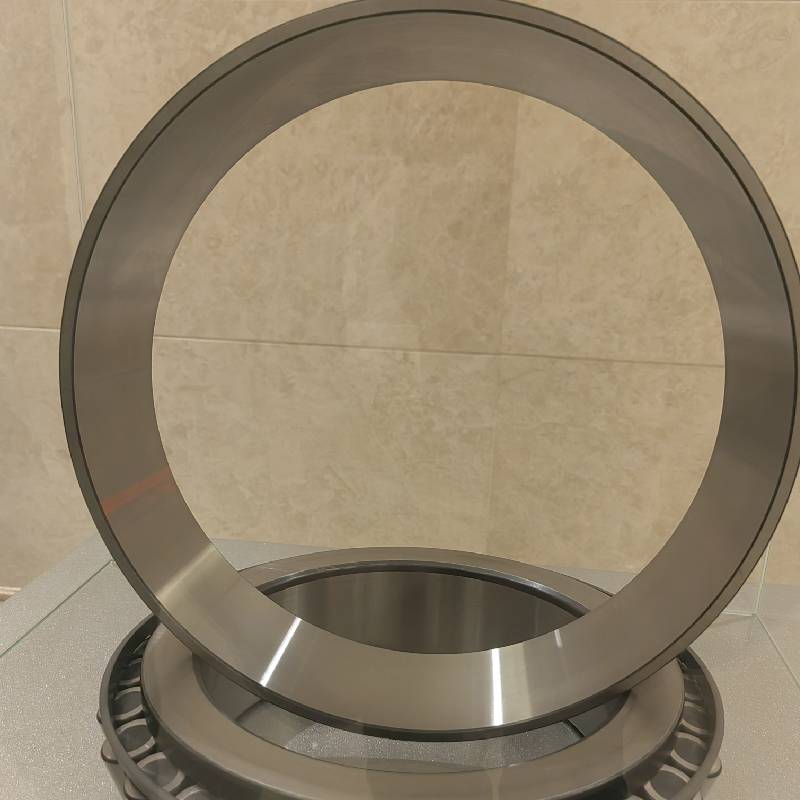
A key aspect of load calculation is recognizing the importance of the dynamic and static load ratings provided by manufacturers. The dynamic load rating determines the bearing’s ability to endure variable conditions over time, while the static load rating sees the maximum load the bearing can handle when stationary. Utilizing these ratings in the calculation process is crucial for selecting the appropriate bearing for your application.
It’s also essential to consider the equivalent dynamic and static bearing loads. For dynamic loads, the calculation considers factors like the bearing’s speed, the nature of the load (constant or variable), and operating conditions. In contrast, static load calculations focus more on load duration and maximum stress scenarios.
Understanding these load dynamics is critical for proper bearing selection. For instance, selecting a bearing with a higher load capacity than necessary can lead to inefficient performance and increased costs. On the other hand, selecting a bearing with insufficient load capacity can lead to premature bearing failure, causing potential downtime and additional costs.
deep groove ball bearing load calculation
Besides theoretical calculations, real-world testing and monitoring can further validate load assumptions. This involves using tools and sensors to measure the bearing's performance under operational conditions. Testing allows for adjustments in the bearing choice or design, ensuring optimized functioning.
Design considerations also include environmental factors, such as temperature ranges and potential contamination. Bearings in environments with extreme temperatures or high levels of debris may require special seals or lubrication to maintain performance under load conditions. Ensuring the right lubrication is present can significantly impact the load-bearing ability and life span of the bearing.
For more in-depth analysis, consulting with a bearing expert or engineer can provide insights tailored to specific applications. These experts bring practical experience, which can be invaluable, especially in unique or demanding operating environments.
Suppliers and manufacturers often provide useful resources, including calculation guides and technical support, which can enhance understanding and execution in load calculation tasks. Those looking to excel in bearing applications should take advantage of these resources to complement their expertise.
Trust and authority in bearing load calculations are established through rigorous testing, continuous monitoring, and adapting to the latest technological advancements. By ensuring that every aspect of load calculation is addressed, from design considerations to operational factors, companies can achieve not only optimal performance but also establish a reputation for reliability and expertise in their respective industries.