Deep groove ball bearings are among the most versatile types of bearings, offering a broad array of applications and numerous advantages for various industries. Their unique design makes them suitable for handling radial and axial loads, an essential characteristic that sets them apart from other bearing types. In this exploration of deep groove ball bearing load types, we will delve into the nuances that make these components indispensable, spotlighting their functionality and the situations in which they truly excel.
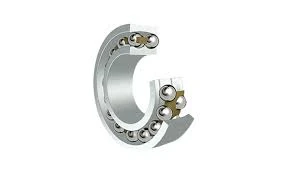
At the heart of a deep groove ball bearing's popularity is its ability to manage both radial and axial loads. Radial loads, the most prevalent type of load, are perpendicular to the axis of the shaft, while axial loads are parallel. The inherent design of deep groove ball bearings allows them to accommodate substantial radial loads due to the deep grooves that interact with the balls. This feature ensures that, even under significant radial pressure, the rotational performance remains smooth and uninterrupted.
Equally impressive is their capacity to withstand axial loads, which, although typically secondary, are sometimes crucial to specific applications. This dual capability is particularly evident in high-speed operations where stability and low vibration are essential. The suitability of deep groove ball bearings in high-speed environments is attributable to their precision-engineered raceways and the high-grade material used in their construction, which minimizes friction and dissipates heat effectively. Industries such as automotive, aerospace, and industrial machinery have seen marked improvements in efficiency and longevity through the use of these bearings.

In terms of expertise, the deployment of deep groove ball bearings requires a detailed understanding of the specific load types and conditions they will encounter. Selecting the appropriate bearing involves considering the load capacity, the speed at which it will operate, and the environmental conditions, such as temperature and exposure to contaminants. These factors are critical in ensuring the bearing performs optimally without premature wear. For environments exposed to moisture or particles, seal or shield options can be implemented to enhance longevity and reliability.
deep groove ball bearing load type
Authoritativeness in the discussion of deep groove ball bearings also encompasses the consideration of material choice. The bearings are commonly constructed from high-grade steel, known for its durability and resistance to deformation under load. For specialized conditions, such as those found in corrosive environments, stainless steel or ceramic ball bearings might be utilized. These materials, although more costly, provide enhanced performance characteristics tailored to the requirements of niche applications.
Trustworthiness is built into the brand and manufacturing process of deep groove ball bearings. Opting for bearings from established manufacturers ensures adherence to strict quality standards, such as ISO and DIN specifications. These standards guarantee that the bearings have undergone rigorous testing in both simulated and real-world scenarios, providing the user with a dependable product. Regular maintenance checks and adherence to recommended installation protocols further ensure these bearings operate optimally for their intended lifespan.
In summary, deep groove ball bearings offer unparalleled versatility through their ability to handle both radial and axial loads effectively. Their design is optimized for seamless integration in high-speed and demanding applications across various industries, backed by a wealth of expertise, authoritative knowledge, and a foundation of trustworthiness. For component selection, understanding the specifics of the operational environment, coupled with rigorous adherence to quality standards, ensures these bearings meet the exigencies of their applications with consistent performance and reliability.