Deep groove ball bearings are frequently utilized across various industries due to their ability to handle radial loads and a subset of axial loads. The material composition of these bearings plays a crucial role in their performance, durability, and application suitability. Choosing the right material is essential for ensuring optimal functionality and reliability in mechanical operations. This article explores the different materials used in the production of deep groove ball bearings, assessing their specific properties and benefits to provide a comprehensive guide for decision-making.
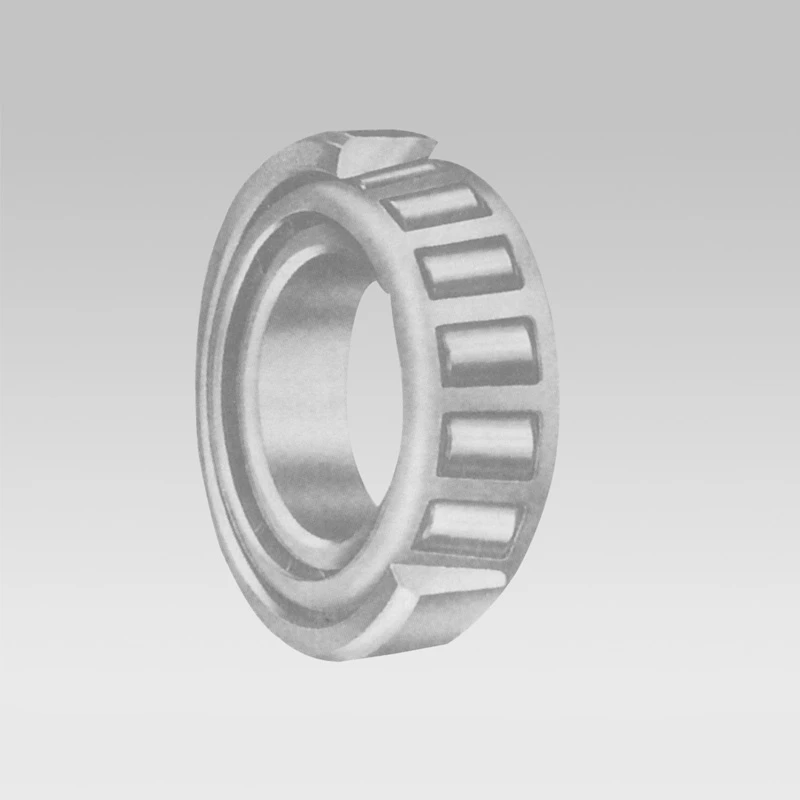
Steel is perhaps the most commonly used material for deep groove ball bearings. Standard bearings are typically made from chrome steel, which is prized for its balance of performance characteristics, including hardness, strength, and resistance to wear and tear. AISI 52100 (also known as 100Cr6) is a typically utilized steel variant due to its remarkable fatigue strength and capacity to withstand significant stress. This type of steel allows bearings to maintain their structural integrity under varying mechanical pressures, making them suitable for high-speed and precision applications.
For environments where enhanced corrosion resistance is necessary, stainless steel bearings are an excellent choice. These bearings are an ideal solution in environments exposed to moisture, chemicals, or salt spray, such as marine environments or food processing plants. Stainless steel, specifically grade AISI 440C, is known for its anti-corrosive properties, while still delivering adequate mechanical performance. It withstands higher degrees of exposure to corrosive elements while maintaining the required durability and load-carrying capabilities.
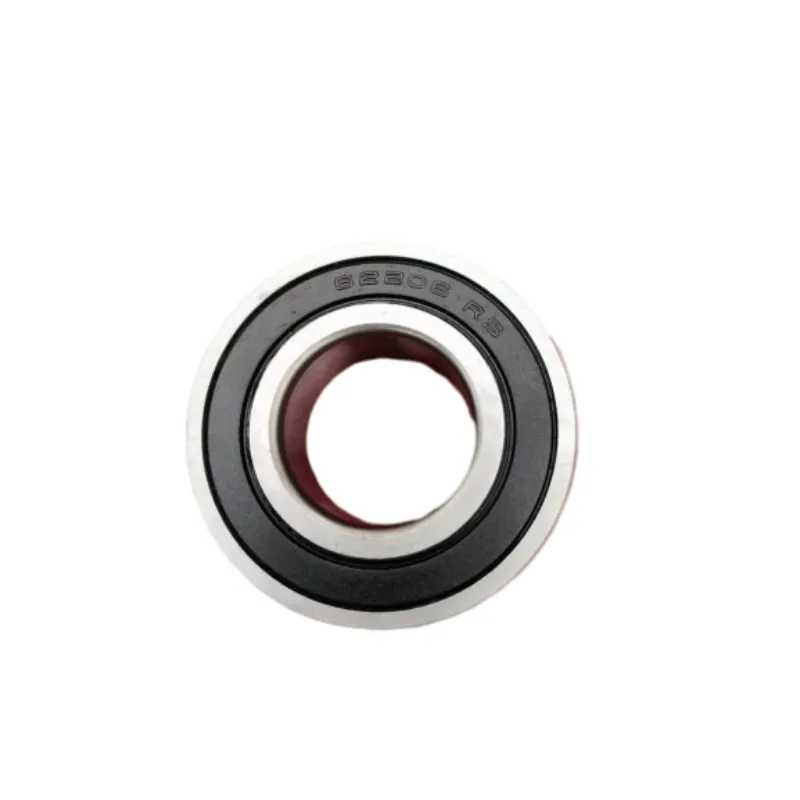
For applications demanding severe conditions or where magnetic properties are concerning, ceramic hybrid bearings offer an innovative alternative. In these bearings, the rolling elements are comprised of ceramic materials such as silicon nitride or zirconium dioxide, paired with steel races. Ceramics provide electric insulation and are lighter than steel, which reduces operational inertia, particularly beneficial for high-speed applications where minimizing rotational drag is crucial. Furthermore, ceramic materials exhibit high temperature resistance and maintain performance consistency across fluctuating temperatures.
deep groove ball bearing material
Another specialized option involves utilizing polymer ball bearings. These are constructed from advanced plastics and offer a lightweight, maintenance-free solution with good chemical resistance. Ideal for applications demanding low friction and where lubrication is impractical, polymer bearings excel in environments involving food processing, laboratory equipment, or cleanroom applications. While they do not match the load-carrying characteristics of steel or ceramic variants, their non-conductive nature and inherent resistance to chemical attack are advantageous in specific niche applications.
The choice of deep groove ball bearing material ultimately depends on the specific operational requirements, environmental conditions, and the type of loads the bearing will encounter. Each material offers distinct advantages that can be maximized in the right context. Engineering teams should perform a thorough analysis of application demands, including speed, load, temperature range, and exposure to environmental factors, to determine the most suitable bearing material.
In summary, the performance and reliability of deep groove ball bearings are significantly influenced by the material from which they are made. Steel remains the go-to material for general applications due to its strength and fatigue resistance. For hostile environments where corrosion is a concern, stainless steel provides enhanced protection. Where electric insulation or reduced weight is essential, ceramic hybrids offer distinct advantages. Meanwhile, polymer bearings cater to specialized applications where traditional materials may not suffice. By aligning material properties with application requirements, industries can optimize bearing performance, thereby improving machinery lifespan and reducing maintenance costs, enhancing operational efficiency.