Groove ball technology, though often overshadowed by more mainstream mechanical components, represents a significant leap in innovation for various industries, enhancing performance and extending the lifespan of machinery. The nuanced design of groove balls combines engineering precision with practical application, offering advantages that are critical yet often underappreciated.

The fundamental concept of a groove ball revolves around its unique ability to reduce friction while maintaining structural integrity under pressure. This feature is primarily attributed to its ingenious design where the groove serves as a pathway that allows for smoother motion and distribution of loads. This engineering marvel enhances the performance of devices by minimizing wear and tear, thus significantly extending their operational life.
In practical applications, groove balls are found in an array of machinery, from automobiles to industrial machines.
Their role in the automotive industry is particularly notable. Within the suspension systems of vehicles, groove balls facilitate enhanced shock absorption. This not only leads to a smoother driving experience but also reduces the stress on other components of the vehicle, thereby decreasing maintenance costs over time.
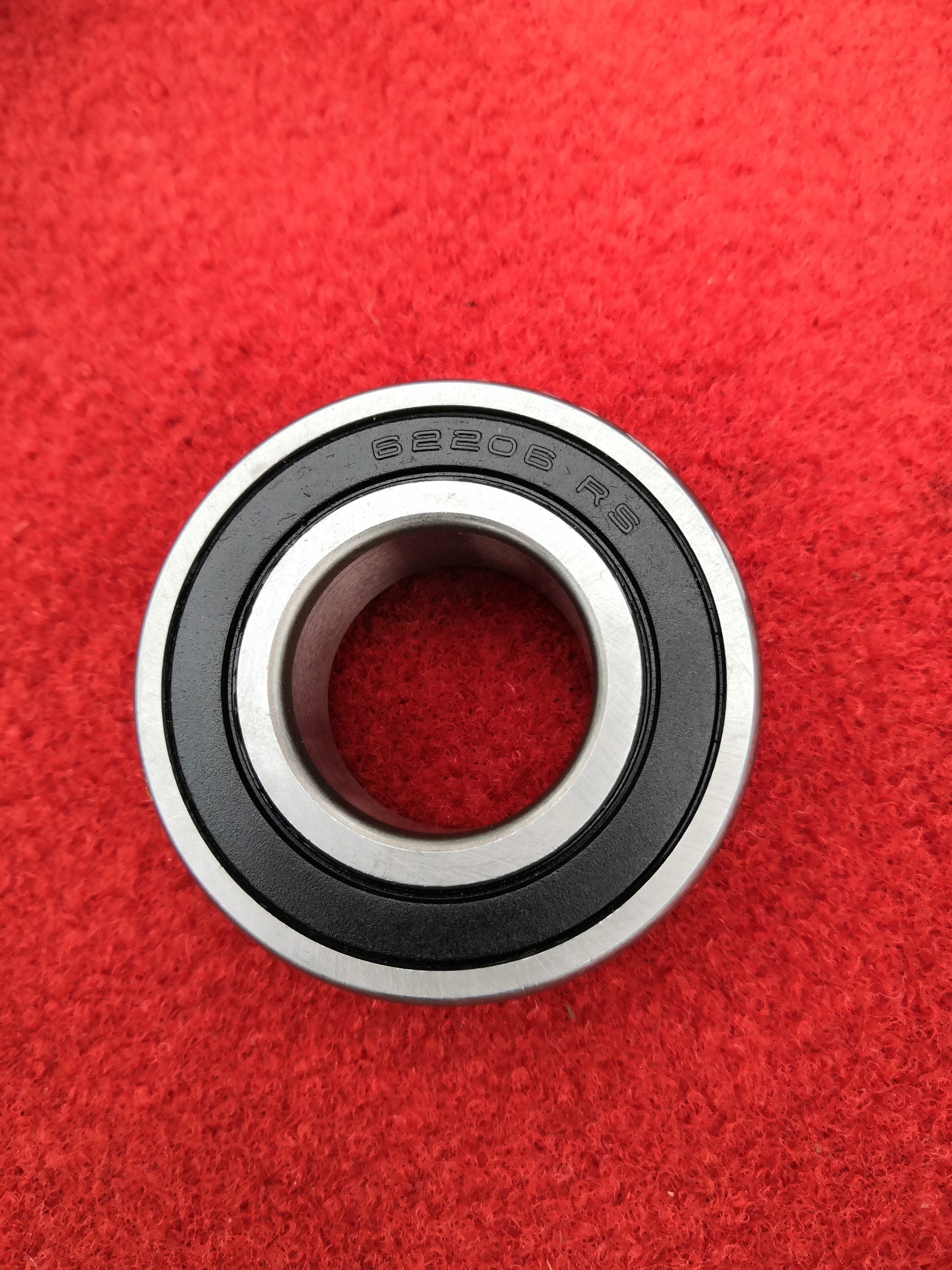
Industrial machinery benefits equally from groove ball implementations. In high-stress environments where equipment is subject to continuous operation, the efficiency of groove balls in bearing loads means less frequent replacements and a reduction in operational downtimes. This reliability is crucial for maintaining productivity and ensuring the seamless operation of manufacturing processes.
Beyond durability and performance, groove balls also contribute to energy efficiency. By significantly reducing friction, these components allow for the smoother operation of engines and motors, translating to less energy required to maintain output levels. This characteristic not only supports sustainability efforts but also aligns with global energy-saving initiatives, making it a critical component in environmentally-conscious businesses.
groove ball
Crafting groove balls requires a high degree of expertise. Professionals in the field must have an understanding of both material science and mechanical engineering. The selection of materials—from high-strength steel to advanced polymers—dictates the performance and longevity of the groove balls under various conditions. Furthermore, precision in manufacturing processes, such as milling and finishing, ensures that each groove ball meets stringent industry standards for quality and performance.
Given the specialized nature of groove balls, manufacturers need to implement strict quality control measures. Testing procedures that simulate real-world conditions are crucial for assessing the durability and functionality of groove balls before they are integrated into broader systems. This meticulous approach not only assures users of the reliability of the product but also builds trust in the brand producing them.
In conclusion, the groove ball may be a relatively understated component, but its contributions to technology and industry are profound. As machinery continues to evolve towards greater efficiency and sustainability, the role of precision components like groove balls becomes ever more vital. Understanding their capabilities and applications not only aids in optimizing machinery performance but also underscores the essential nature of innovation in engineering. Businesses keen on gaining a competitive edge would benefit from integrating such advancements to foster improved operational efficiencies and uphold industry benchmarks.
The nuanced understanding of groove balls and their applications places emphasis on both the expertise of the manufacturers and the indispensability of their role in forward-thinking industrial strategies. As sectors seek optimization in an ever-competitive global marketplace, the investigation and utilization of such innovative components are not just beneficial—they are imperative.